Restauration d'un moteur 15/6
Restauration d'un moteur 15/6
Bien entendu, cet article est hors sujet de ce blog qui n'a que la prétention de faire entretenir sa Traction au quotidien par son propriétaire.Toutefois, cette aventure de la restauration d'un moteur de 15/6 mérite d'être partagée, car elle fera peut être naitre chez le lecteur l'envie de "se lancer" dans quelque chose de plus ardu que le simple entretien. Elle se veut aussi didactive, et bien que ne prétendant pas donner la méthode absolue et exacte pour restaurer un moteur, elle indiquera certainement le fossé qui peut exister entre un moteur réellement refait et un simple "retapage" comme on en voit malheureusement trop souvent...
Tout commence par le déshabillage de l'avant de la voiture, précédé et accompagné de maintes photos qui seront fort utiles pour des détails de remontage.
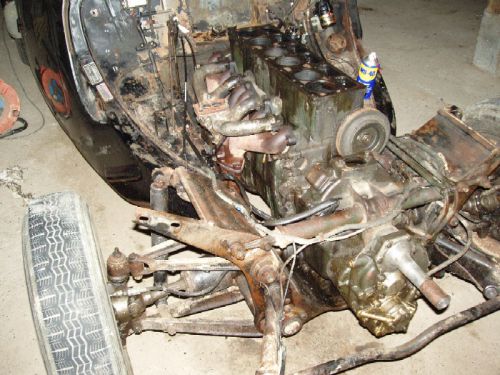
On démonte également les périphériques (carburateur, pompe, dynamo, etc...) pour ne pas les abimer et la culasse pour alléger l'ensemble

Ensuite, on arrime TRES SERIEUSEMENT le tout et il ne reste plus qu'à effectuer la dépose après déconnexion de tout le câblage et des transmissions.
Ensuite, désaccoupler la boite puis procéder au démontage du moteur en repérant soigneusement toutes les pièces qui doivent l'être.
C'est ici que l'on reçoit son lot de bonnes et mauvaises surprises...
Ce moteur présente une excellente ligne d'arbre, des chemises/pistons H.S. mais a également souffert d'une importante corrosion interne par passage d'eau dans l'huile suite à claquage du joint de culasse.
Arbitrairement, il est choisi de commencer par le haut: la culasse.
Celle ci est soigneusement nettoyée, puis entièrement démontée et inspectée.
Les chambres de combustion et les conduits d'admission et échappement sont soigneusement décalaminés.

Après examen des pièces, il est décidé de changer en neuf:
-Les 12 soupapes
-Les 12 guides
-Les 12 ressorts intérieurs
-L'axe des culbuteurs
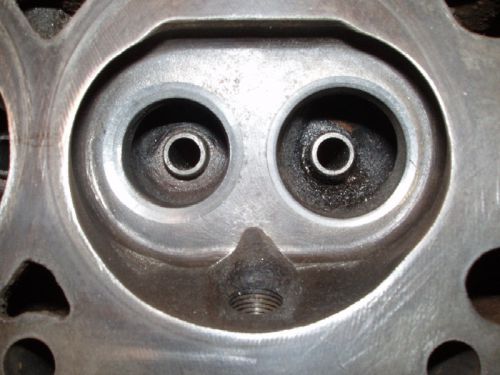
Les guides sont extraits à la presse, remontés de la même manière, puis alésés soigneusement, leur montage entrainant un certain rétreint.
Les sièges de soupapes sont fraisés, mis à la bonne côte en largeur puis les soupapes subissent un léger rodage, très rapide du fait que les sièges sont rectifiés.
Enfin, la culasse est confiée à un atelier professionnel pour être surfacée.
La culasse est maintenant prête pour le remontage, les bouchons de dessablage, en bon état, sont conservés:
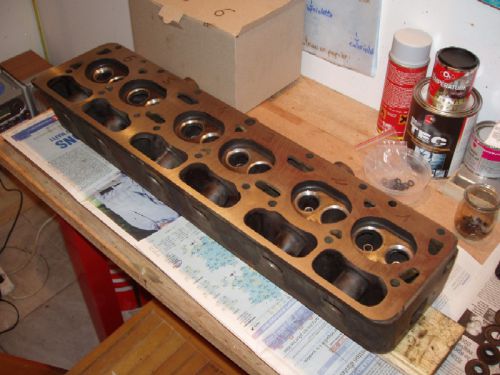
Avec des pièces neuves ou soigneusement nettoyées, abondamment huilées au montage.
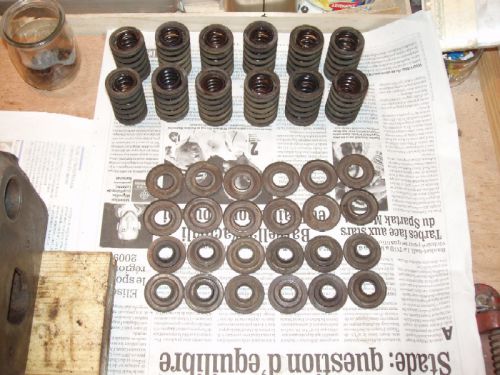
Une fois le remontage terminé, bien huiler l'ensemble pour éviter le retour de la corrosion.
Les culbuteurs (identiques à ceux des 4 cylindres) sont vérifiés et ceux qui ont trop de jeu sont éliminés au profit d'exemplaires à la bonne côte.
L'axe neuf est monté, joints neufs sous les colonnettes et arrêtoirs neufs.
Les écrous de rampe sont serrés au couple.

Culbuteurs bien alignés, comme pour la parade
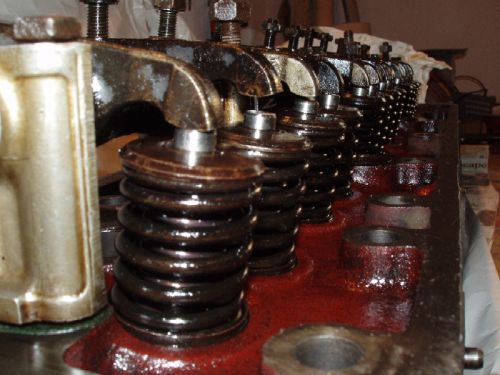
Il est temps de ranger soigneusement notre culasse rénovée, puis de passer à la suite des opérations...
On va s'intéresser maintenant aux bielles:
Les bielles d'origine, régulées, sont écartées au profit de bielles d'ID.
Celles-ci ont l'important avantage de permettre le montage de coussinets minces, moins onéreux qu'un régulage difficile pour lequel les artisans capables sont rares.
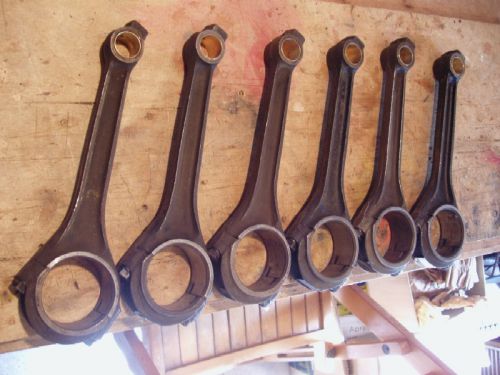
Elles sont équilibrées en poids, équerrées et leur pied est re-bagué et alésé à la côte des axes neufs de pistons par un atelier professionnel. Ce travail est hors de portée de l'amateur...
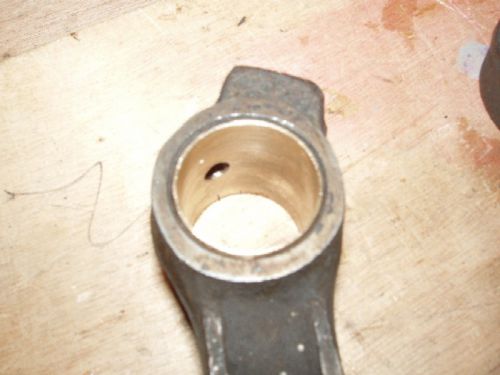
Une fois les bielles rénovées, il est grand temps de s'occuper du vilebrequin.
Il subit en préambule un nettoyage poussé EN PARTICULIER dans les conduits d'huile internes.
Ensuite, il est confié à un professionnel qui jugera la côte de rectification à lui donner.
Il faut lui fournir les coussinets d'arbre, commandés en fonction de la côte déterminée, et ceux de bielles pour faire un travail correct.
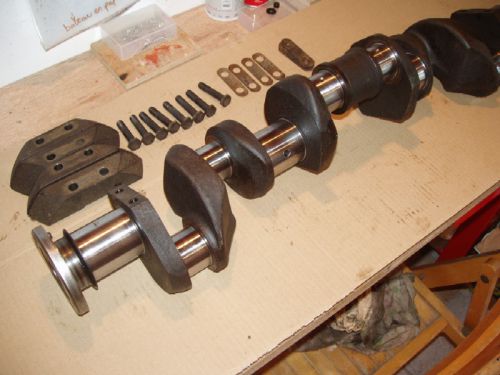
C'est une magnifique pièce qu'on récupère "un certain temps" plus tard...
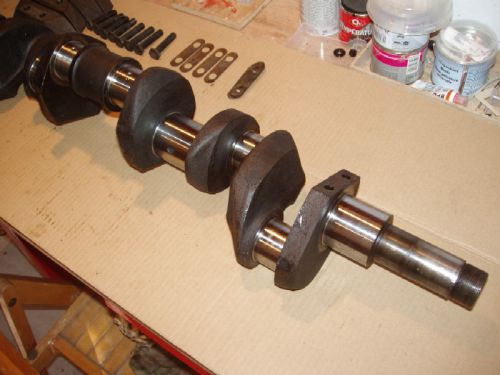
C'est également la pièce mobile la plus lourde (26Kgs) qu'on puisse trouver sur un moteur de Traction...
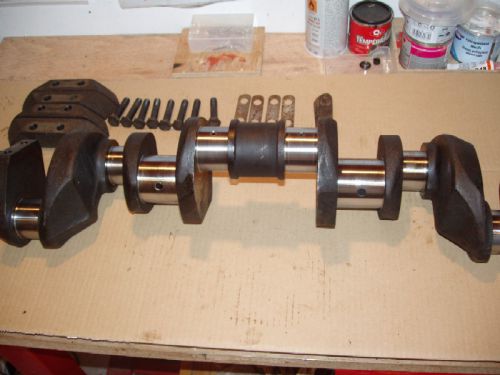
On ne s'attendrit pas trop quand même, et on en profite pour penser à changer le roulement pilote d'arbre primaire de boite à vitesses à l'avant du vilebrequin.
On remonte également les masses d'équilibrages soigneusement repérées au démontage.
On vérifie encore une fois, bielles montées, le bon équerrage de celles-ci: Pas le moindre vrillage ni flambage, c'est parfait, l'ajusteur a bien travaillé.
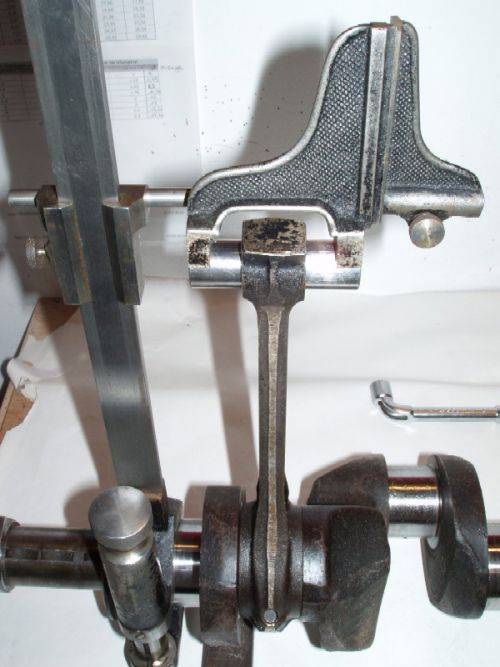
C'est fini pour le vilebrequin qu'on range soigneusement (bien protégé de la corrosion par une fine couche de graisse).
L'arbre à cames est irrécupérable, trop oxydé. Cette pièce n'existe pas en refabrication, il faut donc se mettre en quête d'un arbre d'occasion, en bon état.
Divers avis de professionnels convergent pour attester que l'acier utilisé pour les arbres à cames de traction avant est sensible à la corrosion.
Au premier plan, l'ancien arbre, au second celui qui sera retenu pour le montage.
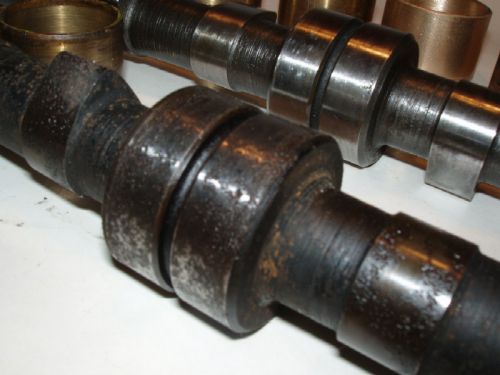
Sur certaines cames, c'est encore plus effrayant:
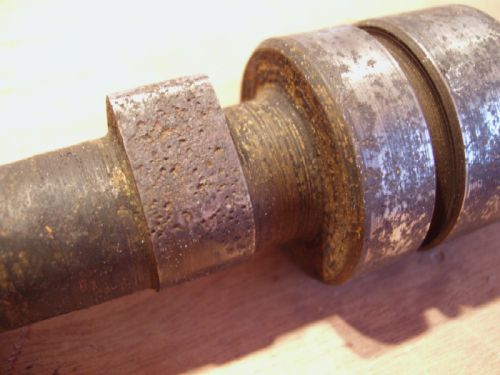
Occupons nous maintenant du bloc...
Pour le nettoyage, plusieurs litres d'essence seront nos alliés afin de venir à bout de 60 ans de cambouis et crasses divers.
C'est un gros travail, très salissant et rebutant.
On finit au nettoyant pour freins en bombe, en particulier dans les conduits d'huile pour bien les décaper.
Ensuite, de longs moments au nettoyeur à haute pression finiront les détails oubliés dans la première phase.
On obtient un bloc tout propre:
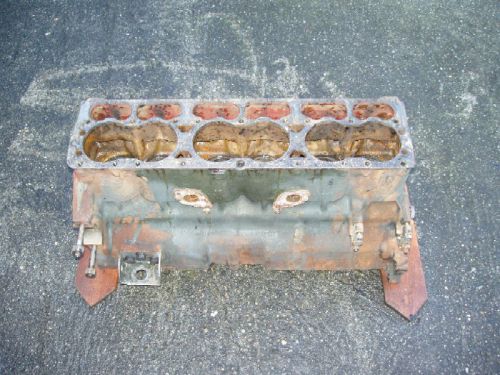
Mais on n'est pas au bout de nos peines, et le travail à faire sur le bloc est encore conséquent:
- Inspection très attentive dans tous les recoins afin de vérifier l'absence de cassures ou de criques
- Vérification de tous les filetages, en particulier ceux des goujons de culasse
- Grattage des chambres d'eau afin de détacher toutes les particules de rouille non adhérentes
- Ebavurage des conduits d'eau. En effet ceux ci présentent des bavures de fonderie restreignant le passage d'eau de manière évidente.
(Comment ça, elle chauffe la 15/6 ?)
Avant ébavurage:

Après: On a gagné facilement environ 15% de la section de passage
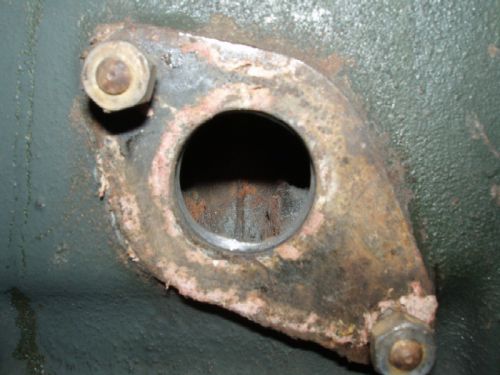
Les chambres d'eau sont alors traitées contre la rouille à l'aide d'un produit dérouillant, à base époxy pour résister à la chaleur:
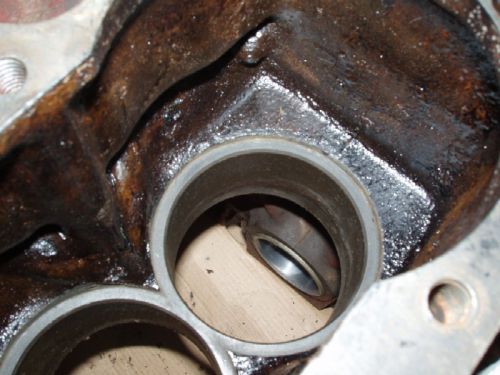
Mais ce n'est toujours pas fini, et il reste à faire un travail capital sur le bloc: Le changement des bagues d'arbre à cames.
Ces bagues sont en effet usées, et surtout ovalisées, remonter le moteur ainsi serait une erreur majeure: perte de pression d'huile, impossibilité de respecter la tension de la chaine de distribution, et certainement un bruit important de fonctionnement de l'arbre à cames.
Sur la photo d'une bague démontée, on aperçoit bien les traces d'usure et d'ovalisation sur les portées.
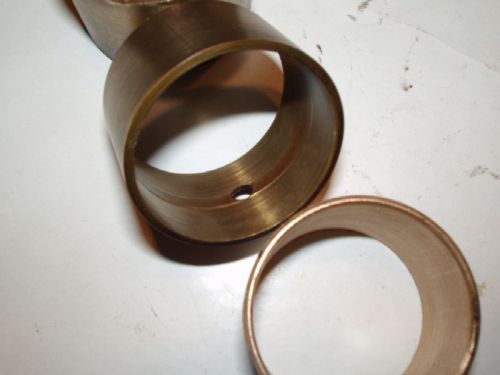
Le bloc prend donc le chemin (bien connu maintenant) de l'atelier spécialisé, et on le récupère re-bagué à neuf, avec un jeu correct au niveau des paliers:
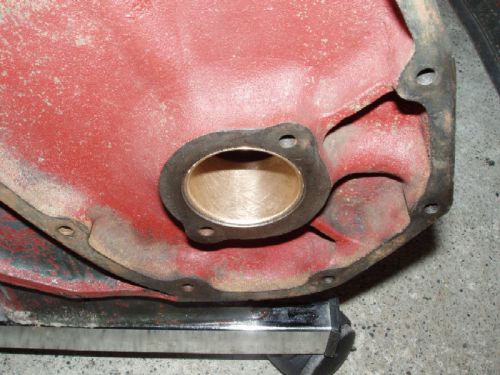
On est sûr du fonctionnement futur, l'ajustage étant fait à l'aide de l'arbre à cames qui sera monté sur ce moteur, bref du véritable sur-mesure !
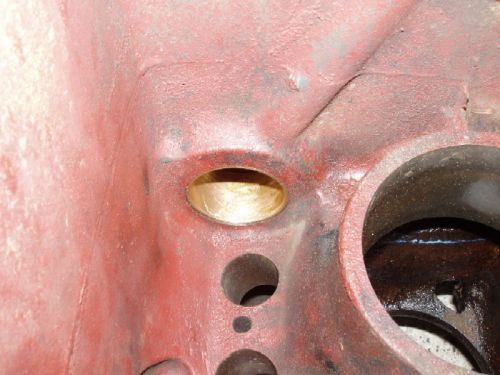
Une fois tout cela terminé, on s'aperçoit qu'approche enfin l'heure du remontage !
Le "point bas" de la restauration du moteur est atteint, la sous traitance spécialisée est finie et tout ce qui va suivre va nous rapprocher du moteur terminé.
Il est temps de placer nos coussinets neufs dans le bloc: un premier serrage léger pour que tout se mette bien à sa place:
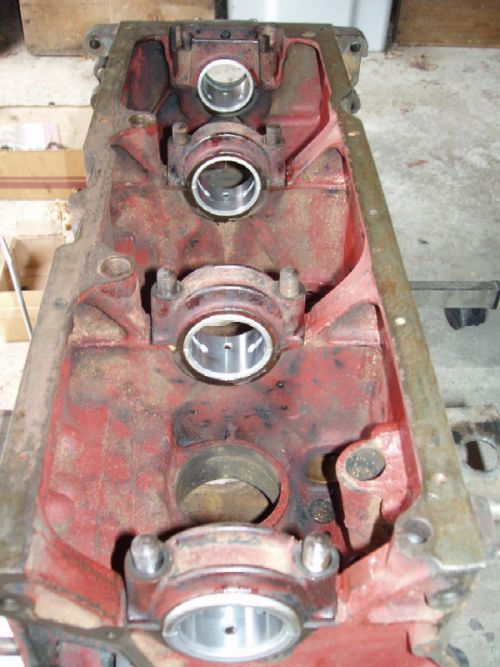
Et on re-démonte pour reposer le vilebrequin dans ses coussinets...moment émouvant:
On remonte les chapeaux de paliers, on les serre au couple et on vérifie la bonne rotation de l'ensemble, sans jeu ni point dur. Dans ce cas précis, l'aléseur a fait du beau travail, le résultat est impeccable.
Il est alors temps de procéder à une opération primordiale pour la bonne tenue de la ligne d'arbre dans le temps, et son silence de fonctionnement: le réglage du jeu latéral du vilebrequin:
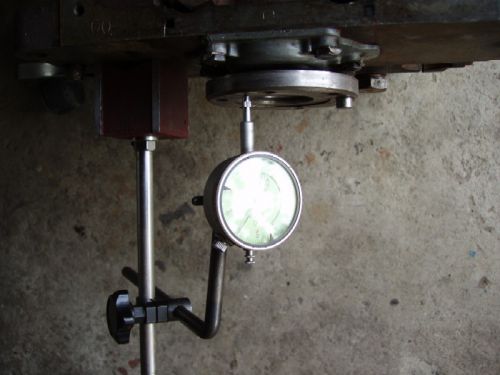
Il se règle à l'aide de cales placées coté distribution, et pour sa mesure précise un comparateur est bien préférable à un simple jeu de cales.
Le constructeur donne une fourchette entre 15 et 20 centièmes.
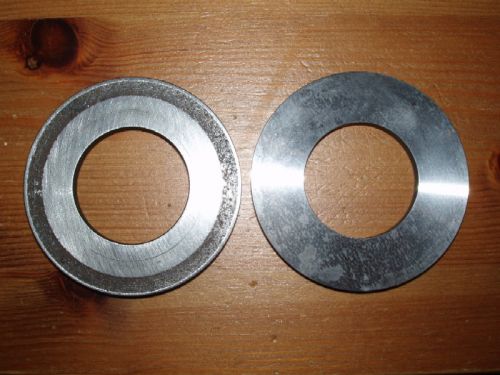
Sur notre moteur, nous obtenons finalement un jeu de 16 centièmes, parfaitement dans les tolérances.
Il est temps maintenant de remonter l'arbre à cames.
On le place, bien huilé dans ses paliers, puis on pose la bride et on serre les vis au couple en ayant soin d'interposer deux arrêtoirs neufs.
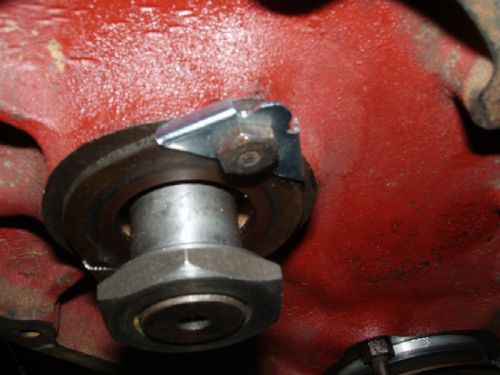
Ensuite, contrôler le jeu longitudinal, pignon de distribution en place et serré au couple. On obtient 0,10 mm, ce qui est acceptable.
Si la bride est trop usée, sur la portée du pignon, monter une bride neuve, mais attention à sa qualité (voir l'article : "les pièces neuves à jeter")
Il est temps maintenant de remonter la commande de la distribution, soit la chaine et ses deux pignons.
Ici, tout est neuf, c'est plus simple. Il est très peu recommandé de panacher à ce niveau des pièces neuves et des pièces anciennes, traditionnellement, l'ensemble se change.
Il faut d'abord aligner les deux pignons, recouverts de la chaine selon les prescriptions du constructeur. La photo parle d'elle même:
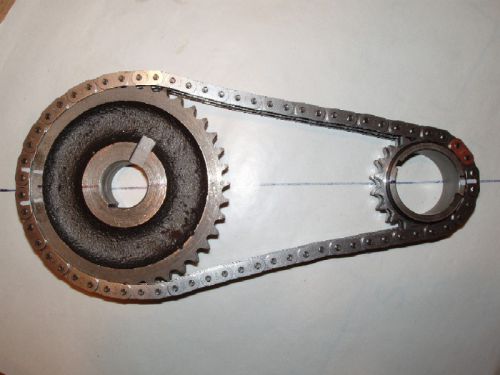
Une droite doit passer par les centres des pignons et les repères de ceux-ci, placés à l'intérieur des pignons.

Bien, maintenant que notre ensemble chaine/pignons est bien aligné, comment le monter sur le moteur ?
Rien de bien compliqué: commencer par aligner le vilebrequin avec les deux cylindres extrêmes au P.M.H. (point mort haut): Cela correspond justement à une position de la clavette de vilebrequin vers le haut.
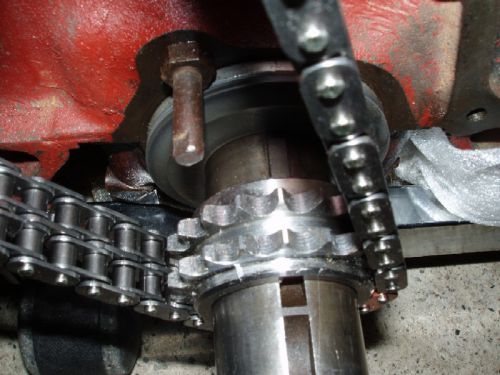
Pour l'arbre à cames, la clavette sera horizontale et dirigée vers la gauche du moteur.
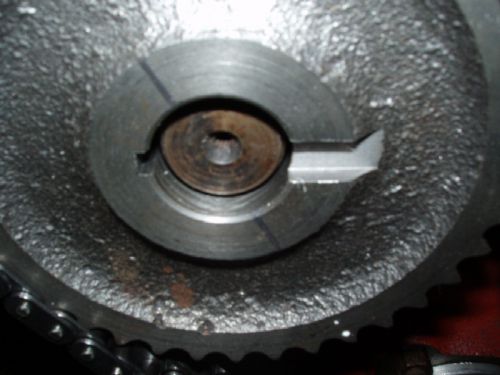
Engager alors doucement l'ensemble chaines/pignons en place, sans faire sauter la chaine. Les repères faits en périphérie des pignons sont utiles pour vérifier qu'on ne se décale pas au montage.
Tourner légèrement l'arbre à cames si nécessaire pour permettre la bonne introduction des pignons bien à fond sur leurs portées. Leur mise en place se fait très progressivement et alternativement, afin de ne pas tordre la chaine et la contraindre. Vérifier que les clavettes sont bien engagées dans les rainures et ne sortent pas de leurs logements.
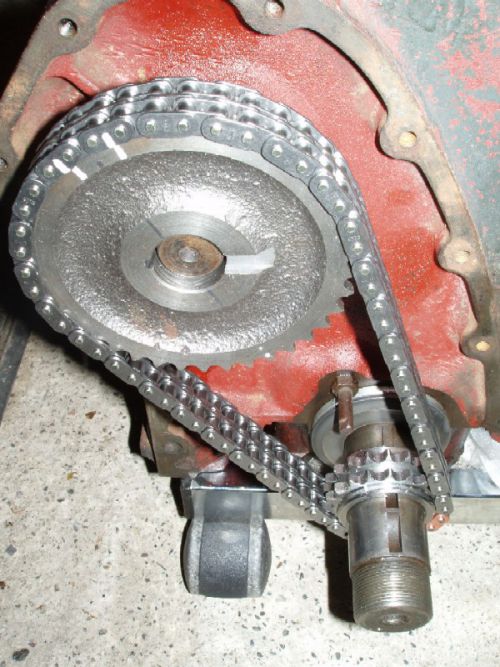
Vérifier encore le bon alignement des repères puis tourner le vilebrequin de plusieurs tours dans un sens puis l'autre. On doit revenir sans souci sur le calage originel.
Placer alors l'arrêtoir d'écrou sur l'arbre à cames, l'écrou et serrer au couple.
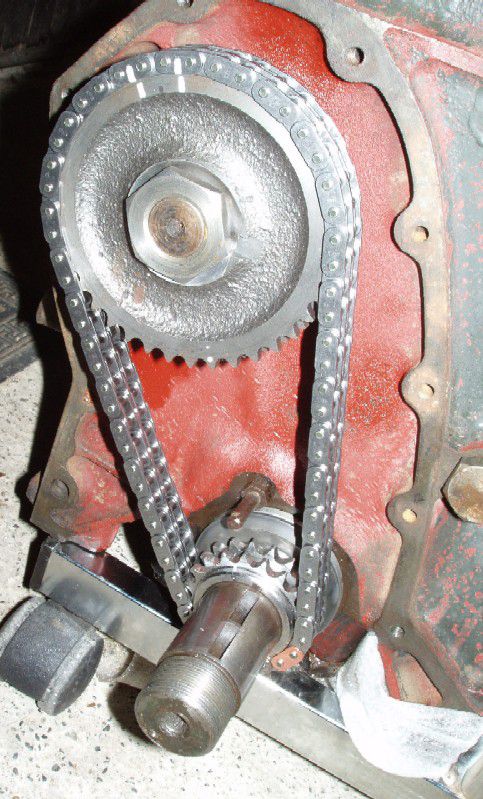
On s'aperçoit que la chaine est parfaitement tendue: suffisamment mais également sans excès, le travail sur les paliers d'arbre à cames prend ici son sens.
Dernière étape: rabattre l'arrêtoir d'écrou:
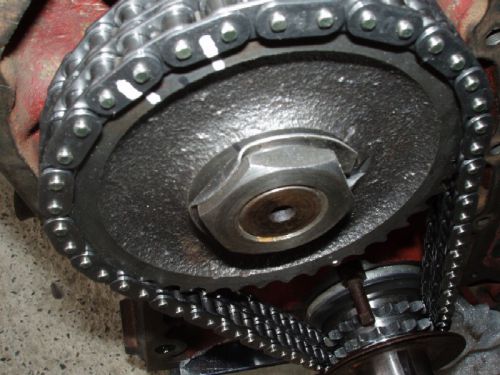
La distribution est alors en place et correctement calée.
Il est temps de cacher tout cela sous le carter de distribution, mais non sans avoir replacé les deux clavettes de vilebrequin, après il sera trop tard pour l'une d'entre elles.
Le carter est prêt, avec son joint neuf que l'on va "enrichir" avec la célèbre pâte HERMETIC. Cette pâte à joints, aussi vieille que la Traction se trouve chez les bons revendeurs de pièces détachées ou encore chez les Shipchandlers.
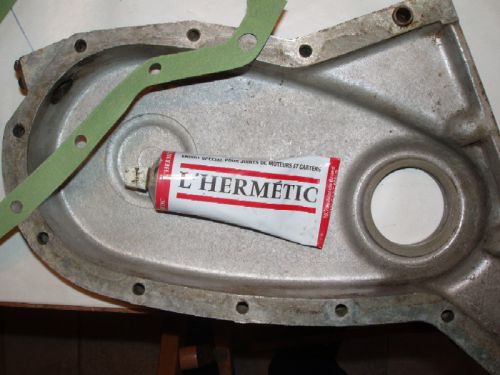
Une fois le joint enduit sur ses deux faces, voilà le résultat: le carter est prêt à la pose.

Placer le carter qui se centre seul grâce à ses deux pieds de centrage, puis l'ensemble des vis et serrer au couple.
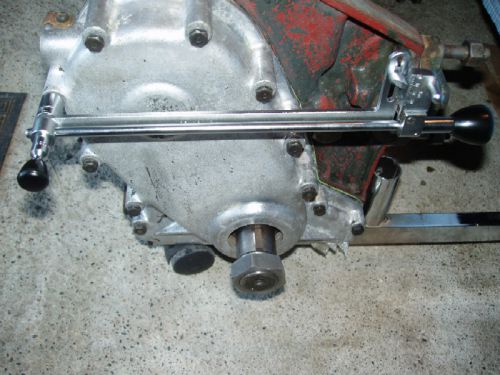
Ensuite, placer la coquille/carter, approcher les 4 vis de fixation et la centrer.
Ici, pour le centrage, il est utilisé un vieux moyeu d'une poulie cassée.
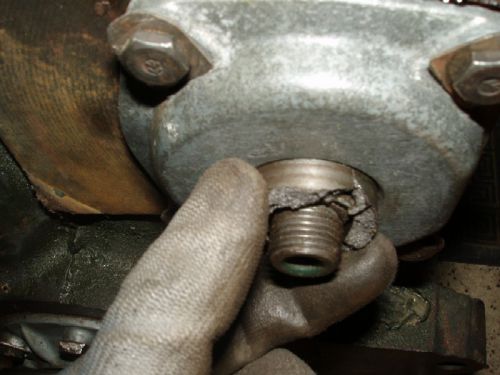
C'est d'une inélégance totale, mais c'est finalement efficace et précis, car le moyeu de poulie ne doit frotter en aucun endroit de la coquille, munie de filets de retour d'huile qui ne doivent jamais être en contact avec la partie tournante, ce qui les déteriorerait irrémédiablement.
Une fois le centrage correctement réalisé, finir le serrage au couple et rabattre les arrêtoirs.
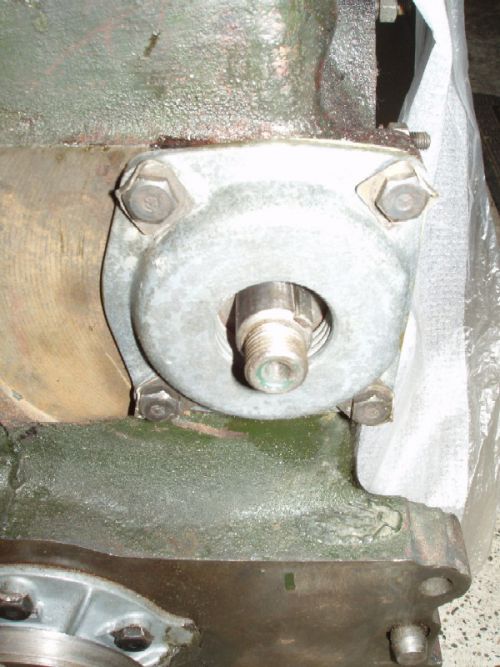
Il est temps maintenant de monter les ensembles chemises, pistons bielles.
Les bielles, et ensembles pistons/chemises neufs ont été soigneusement repérés préalablement pour ne pas être désappariés.
Pour mémoire, on contrôle d'abord le jeu à la coupe des segments, qui doit correspondre aux indications du fabricant (différentes de celles du constructeur à l'époque).
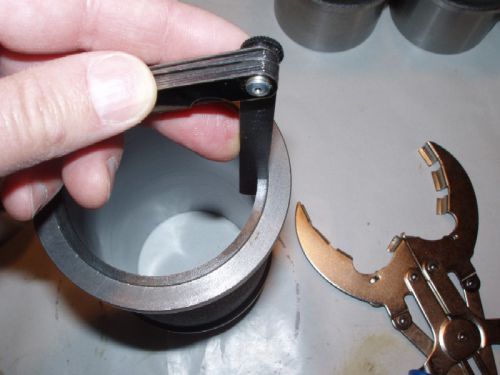
Nous préférons nettement la méthode consistant à monter la bielle sur le piston, le piston dans la chemise, et l'ensemble dans le moteur: en effet, l'engagement du piston par le bas de la chemise, munie d'un chanfrein à cet endroit, est nettement moins dangereux pour la casse d'un segment que par le haut, même avec un bon collier à segments.
La tête de bielle passera facilement par l'embase de la chemise dans le bloc à condition de déposer le chapeau.
Commençons donc par monter les bielles sur les pistons.
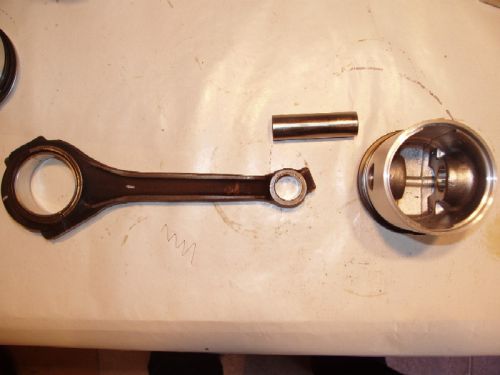
La pose des circlips d'arrêt d'axe de pistons doit se faire en orientant la coupe de manière à ce que le mouvement vertical du piston n'ait pas tendance à l'ouvrir, ni à le faire tourner dans sa gorge:
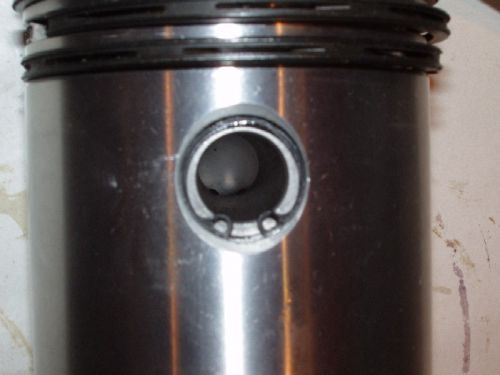
L'axe s'introduit "au pouce" (même si on peut tricher en utilisant l'index, il n'y aura aucune conséquence sur la marche du moteur).
Poser ensuite le deuxième circlips.
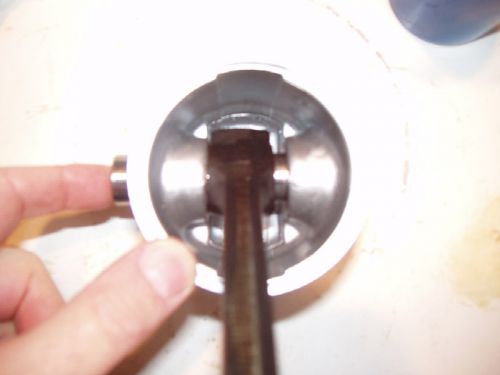
ATTENTION, lors de cette opération d'orienter correctement le piston par rapport aux repères de la bielle pour son montage futur dans le moteur.
S'il est repéré sur sa tête d'une flèche constituée de petits points, elle doit être orientée vers l'arbre à cames.
Si la flèche est constituée de petits tirets, c'est vers l'avant du moteur (coté volant).
On ne peut confondre l'un et l'autre du fait de la position de l'axe, bien évidemment, mais on peut monter le piston à l'envers !
ATTENTION également, si l'on utilise des bielles ID DS ou 11D: La coupe de ces bielles doit impérativement être orientée coté arbre à cames.
Bien vérifier tout cela au cours du montage.
Une fois cette opération répétée 6 fois, on doit obtenir ce genre de chose:
Insistons encore une fois sur l'importance d'un bon repérage de l'ensemble des pièces, seul garant d'un montage correct et facile. Une fois le moteur refermé, il sera bien trop tard...
Prendre garde, lors du repérage, que les méplats des chemises sont alternativement vers l'avant et l'arrière du moteur.
Idéalement, repérer les chemises/pistons neufs par numéros 1-2-3-4-5-6 puis placer les chemises comme on les montera dans le moteur, et repérer le coté arbre à cames (un point blanc par ex) ce qui permettra l'orientation correcte du piston au moment de l'appariement chemise/piston-bielle.
Bien, arrachons nous à la contemplation de ce bel ensemble et passons à la phase suivante: le montage des pistons/bielles dans les chemises.
Auparavant, il faut vérifier le dépassement des chemises du bloc.
Les ensembles modernes sont usinés aux spécifications "11D", c'est à dire qu'il n'y a normalement pas de réglage à faire: La chemise est à une côte de dépassement zéro, et le seul montage du joint papier suffit à assurer la bonne hauteur de dépassement.
On vérifie, et effectivement, montée sans joint la chemise arase juste le bloc:
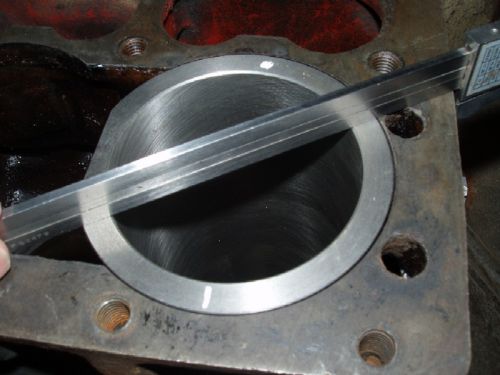
On en profite pour contrôler cela sur chacun des cylindres, et en plusieurs points pour s'assurer du bon état des différentes embases de chemises.
Le joint papier mesure 7 centièmes d'épaisseur, ce qui convient parfaitement pour un dépassement raisonnable.
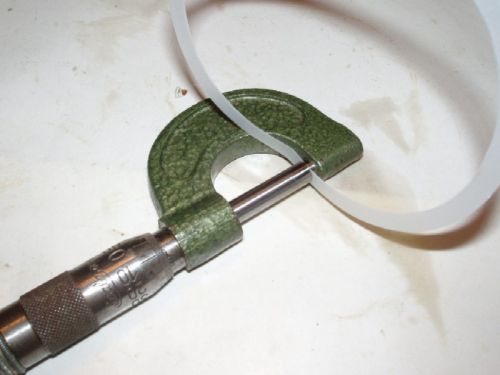
Montage des pistons:

Auparavant, il faut tiercer les segments. Ici, ils sont au nombre de quatre, on va donc les "quarter" ...
On les oriente à 180° l'un de l'autre, légèrement décalés par rapport à l'axe du piston:
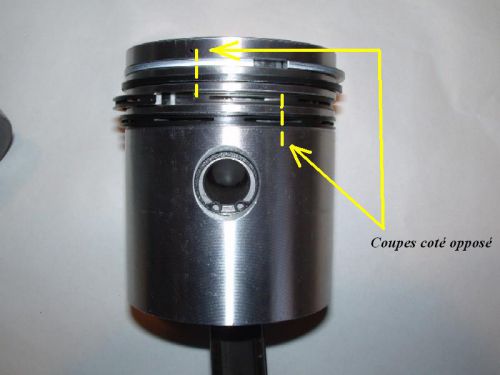
Huiler abondamment la chemise et le piston, après avoir éliminé la cire de protection d'origine.
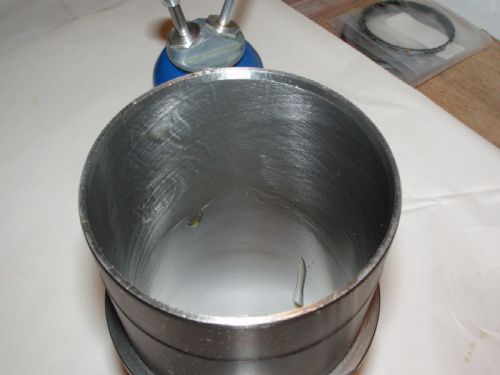
Monter le piston huilé dans un collier à segments. Il est aventureux de se passer de cet outil pour un emmanchement sans risque de casse:

Et il ne reste plus qu'à terminer l'introduction du piston dans sa chemise, en PRENANT GARDE à respecter l'orientation de l'ensemble par rapport à la position future de la chemise en regard de l'arbre à cames.
En procédant à une introduction par le bas, c'est très facile: une poussée sur la bielle suffit pour que tout rentre souplement et sans frapper du fait de l'embase évasée de la chemise. C'est nettement plus sûr que par le haut:
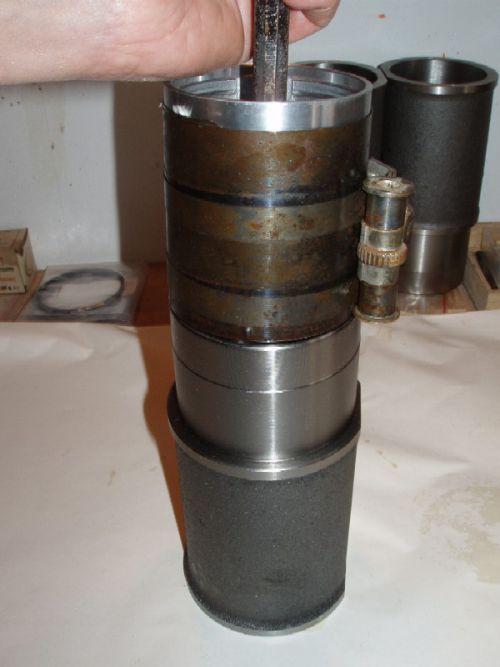
Il est maintenant temps de placer nos ensembles chemises/pistons/bielles dans le bloc.
Avant tout, traquer toute impureté sur les embases !
C'est très important, remonter la chemise sur une embase sale entraînera irrémédiablement des fuites
La préparation est simple, enlever le chapeau de tête de bielle (sinon, elle ne passe pas dans l'embase des chemises sur le bloc) puis mettre un peu d'Hermétic sur l'emplacement du joint.
Ce n'est pas absolument indispensable, mais pas contre indiqué non plus. Par principe, sur un moteur ancien, nous préférons en mettre toujours un peu.

Puis placer le joint en prenant garde de ne pas le déchirer:
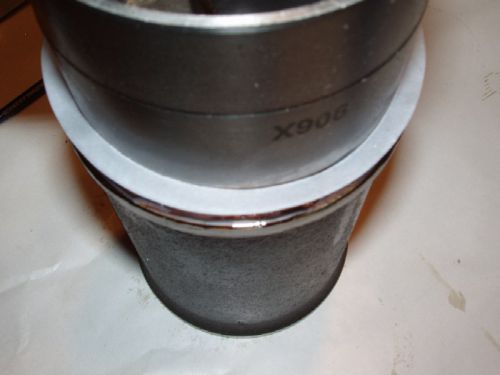
Et enfin, une dernière séance d'Hermétic:
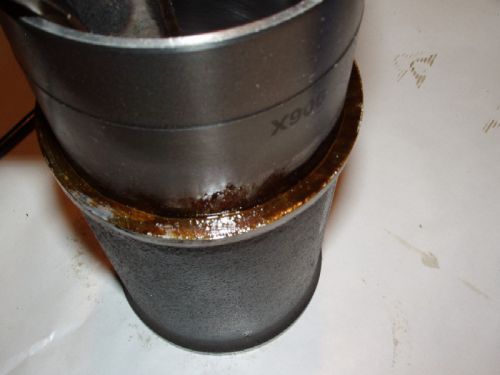
Puis huiler à la burette les paliers de bielle:
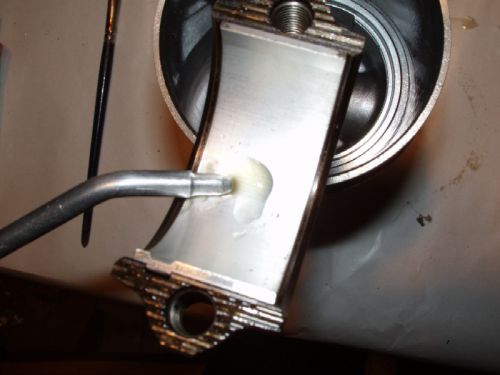
Il ne reste plus alors qu'à insérer la chemise dans le bloc, correctement orientée.
On ne regrette pas ici le temps passé à faire des repères sérieux et cohérents.
Attraper par en dessous la tête de bielle, placer le chapeau de palier dans le bon sens (repères !) et le serrer modérément. On fera le serrage au couple lorsque tous les paliers seront en place.
On monte les chemises par paires, puis elles doivent être immobilisées par des rondelles (par exemple) pour ne pas se décoller de leur embase lors de la rotation du moteur pour attacher les paliers de bielles.
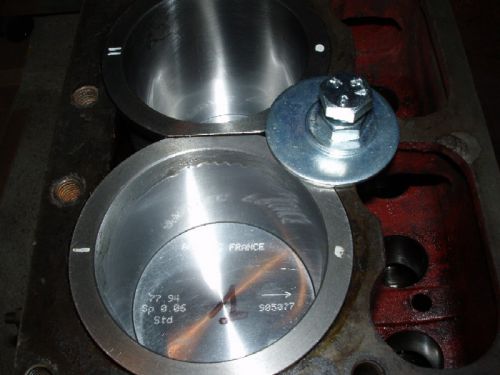
Au fur et à mesure du montage des ensembles, le moteur devient de plus en plus dur à tourner à la main. C'est normal.
On contrôle bien l'orientation correcte de chaque élément, et une fois de plus on se félicite d'avoir tout correctement repéré.
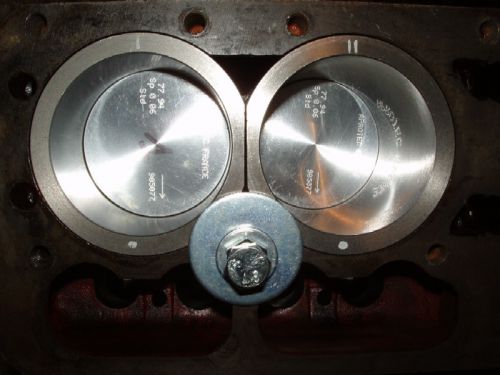
Profitons en pour vérifier la côte de dépassement des chemises au dessus du plan de joint du bloc.
Ici, la cale de 9 centièmes passe bien et la 10 passe gras. Cela se présente pas mal !
Contrôler cela dans plusieurs axes, mais ne pas oublier qu'on travaille sur un moteur ancien aux côtes parfois pas très justes. Ne pas traquer le centième mais vérifier la cohérence de l'ensemble.
Voilà, il ne reste plus qu'à réaliser cette opération 6 fois et on a bel et bien notre bloc enfin prêt à recevoir sa culasse.
Prêt ? pas tout à fait puisqu'il manque les poussoirs.
Chacun, repéré au démontage, est soigneusement nettoyé et vérifié. Ici, les poussoirs d'origine sont encore à la bonne côte et n'ont pas de jeu dans leurs alésages. On les réutilisera donc:
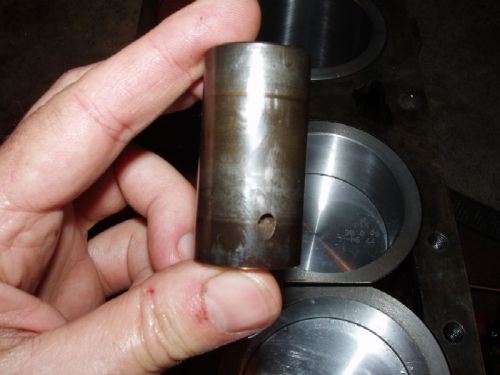
Huilage très abondant, et chacun réintègre son emplacement.
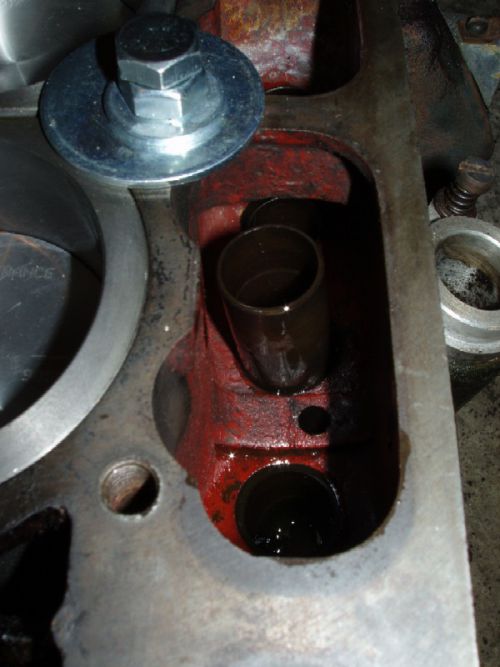
Une fois en place, on vérifie que les 12 coulissent bien librement.
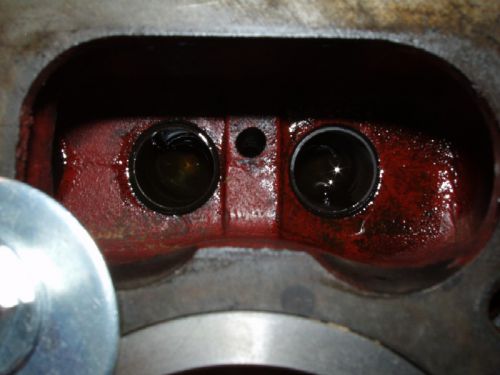
Vérification des goujons et écrous de fixation de la culasse. Si l'on réutilise ceux d'origine, s'assurer que les filetages sont impeccables et bien brossés.
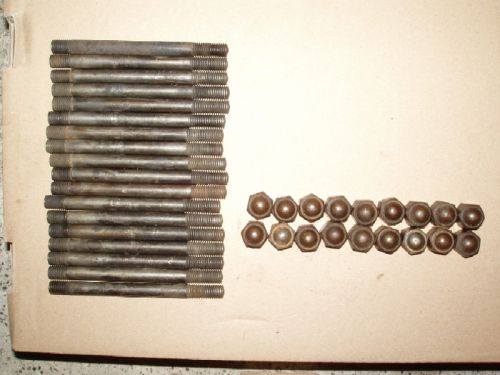
Nous sommes de nature méfiants avec les écrous borgnes pour le serrage des culasses.
Le risque existe que le serrage arrive à fond de filets avant que la culasse soit correctement serrée. Vérifions cela:
Un goujon est mis en place, petit filetage coté bloc, puis l'écrou serré à fond de filet. On vérifie la côte : 94 mm.
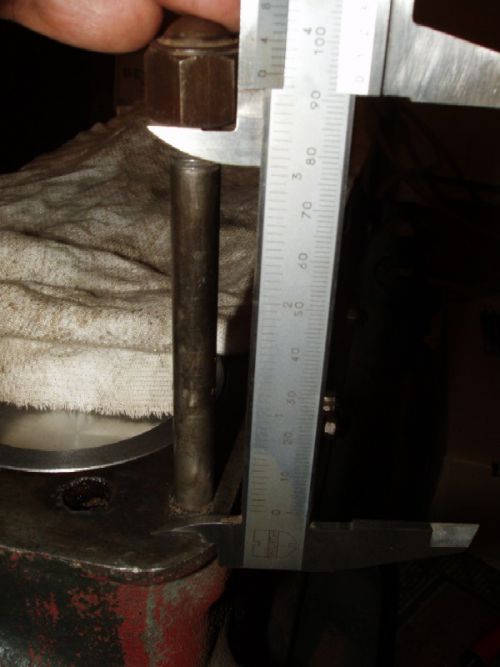
Aïe, c'est exactement la côte d'épaisseur de la culasse. Le joint, non comprimé, fait 2,2 mm et la rondelle d'origine sous l'écrou 1 mm.
Le constructeur a prévu bien juste à ce niveau: Par précaution, nous monterons des rondelles inox de 2 mm, soit un total de marge de 4,2 mm avant d'arriver en fond de serrage, ce qui correspond à un peu plus de 2,5 tours d'écrou.
Remontage des goujons sur le bloc:
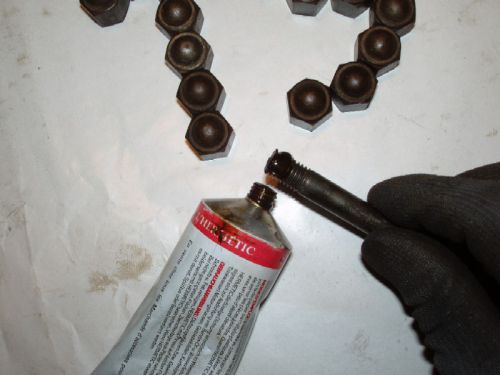
Le petit coté du filetage vient dans le bloc. On l'enduit d'un peu d'Hermétic, puis vissage et serrage au couple (2 m.Kg)
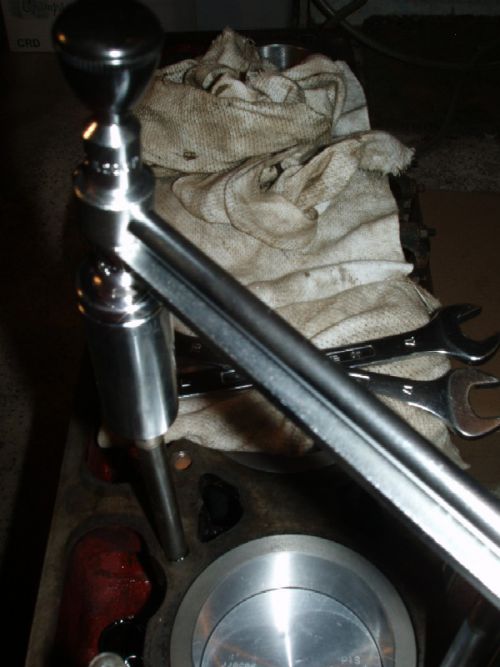
C'est assez long, avec la méthode écrou/contre-écrou, mais on avance la forêt de goujons.
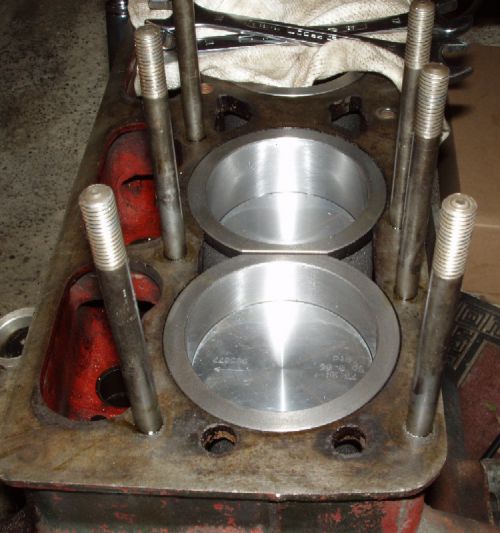
Passons au joint de culasse. Le montage se fera coté lisse vers le bloc et les sertissages vers la culasse.
On vérifie qu'il passe bien sur les goujons et le pied de centrage de la culasse.
On le monte enduit d'huile moteur: Le but est ainsi de favoriser le glissement du cuivre contre la fonte au moment de son écrasement par le serrage des goujons au couple, et d'éliminer toute contrainte sur les minces et donc fragiles pellicules de cuivre entourant la matière isolante du joint.
.
Une fois le joint posé dans le bon sens, placer la culasse, les 18 rondelles et écrous borgnes.
On obtient quelque chose qui ressemble de plus en plus à un moteur de 15/6.
Faire suivre par la séquence de serrage au couple, et dans l'ordre donné par le constructeur, des écrous.
1° serrage à 2 mKg, puis un deuxième à 5 mKg. Réaliser ces opérations très progressivement et en revenant sur le dernier serrage au moins deux fois.
Les filetages ont été préalablement huilés, ainsi que les faces d'appui des écrous.
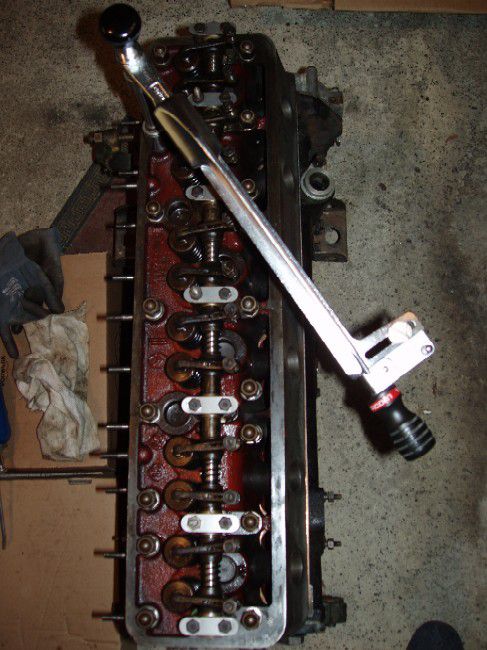
Nous utilisons des rondelles inox de 2mm d'épaisseur, comme indiqué plus haut, afin d'éviter le souci d'arriver à fond de filet avant le bon serrage.
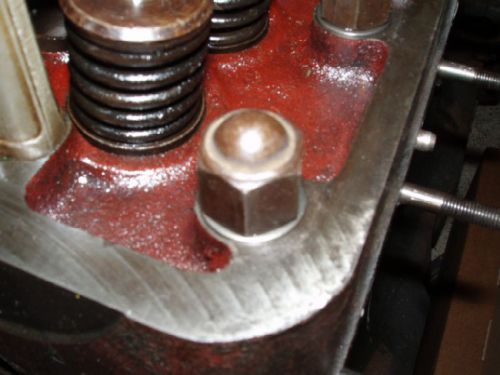
ADDITIF: On s'est un peu inquiété pour rien !
Il s'avère, suite à une info pêchée auprès d'un autre tractionniste passionné, que les écrous borgnes sont des "faux borgnes".
Le dôme de l'écrou n'est pas monobloc, mais est en fait un petit chapeau rapporté, qui saute facilement au serrage à fond de filet. Aucun risque donc, hormis de perdre le chapeau dans le bas moteur, d'avoir un serrage insuffisant. Merci Gérard pour la trouvaille, bien peu doivent savoir cette astuce. Cela n'empêche pas de monter des rondelles inox qui ne s'écrasent pas au serrage.
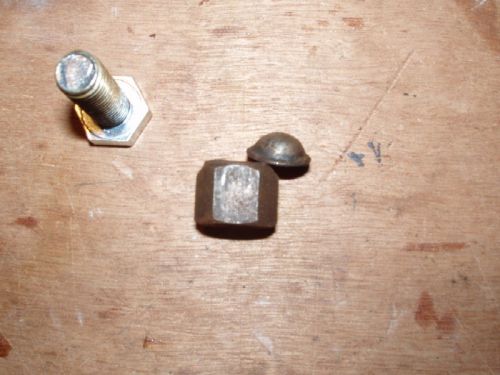
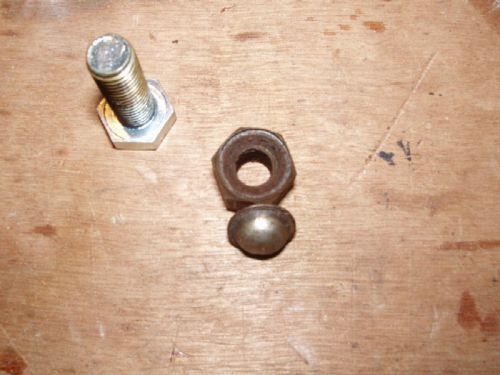
Replacer ensuite les tiges de culbuteurs, repérées au démontage avec une bonne goutte d'huile dans les rotules.
Elles passent très facilement en dévissant à fond les vis des basculeurs.
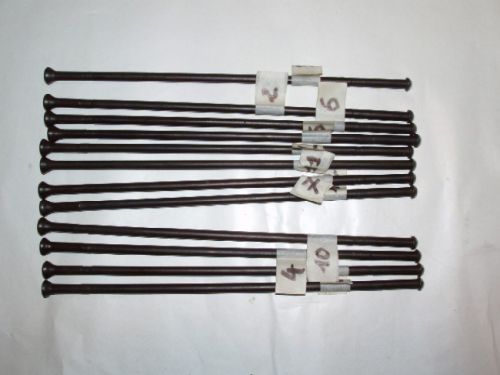
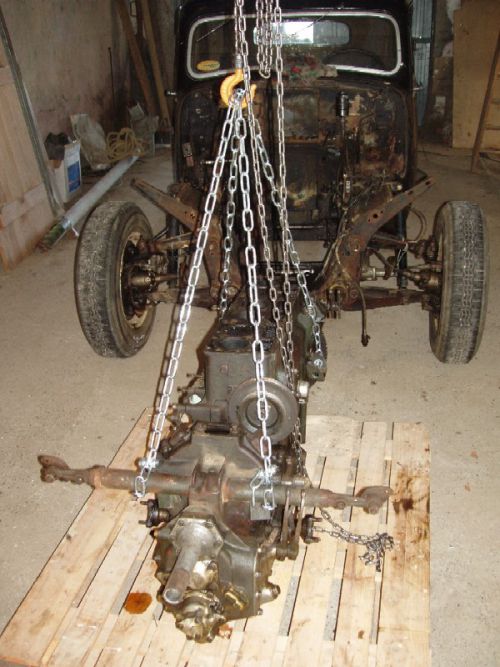
Ensuite, désaccoupler la boite puis procéder au démontage du moteur en repérant soigneusement toutes les pièces qui doivent l'être.
C'est ici que l'on reçoit son lot de bonnes et mauvaises surprises...
Ce moteur présente une excellente ligne d'arbre, des chemises/pistons H.S. mais a également souffert d'une importante corrosion interne par passage d'eau dans l'huile suite à claquage du joint de culasse.
Arbitrairement, il est choisi de commencer par le haut: la culasse.
Celle ci est soigneusement nettoyée, puis entièrement démontée et inspectée.
Les chambres de combustion et les conduits d'admission et échappement sont soigneusement décalaminés.

Après examen des pièces, il est décidé de changer en neuf:
-Les 12 soupapes
-Les 12 guides
-Les 12 ressorts intérieurs
-L'axe des culbuteurs
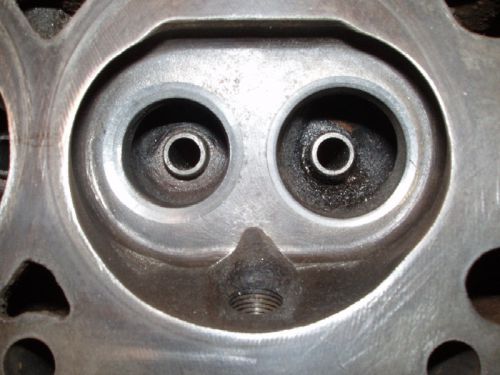
Les guides sont extraits à la presse, remontés de la même manière, puis alésés soigneusement, leur montage entrainant un certain rétreint.
Les sièges de soupapes sont fraisés, mis à la bonne côte en largeur puis les soupapes subissent un léger rodage, très rapide du fait que les sièges sont rectifiés.
Enfin, la culasse est confiée à un atelier professionnel pour être surfacée.
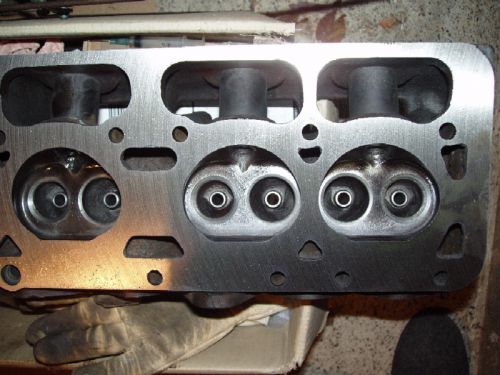
La culasse est maintenant prête pour le remontage, les bouchons de dessablage, en bon état, sont conservés:
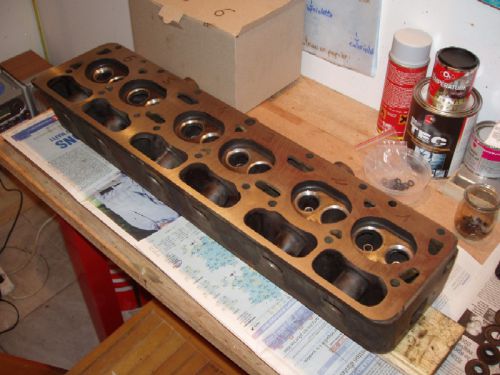
Avec des pièces neuves ou soigneusement nettoyées, abondamment huilées au montage.
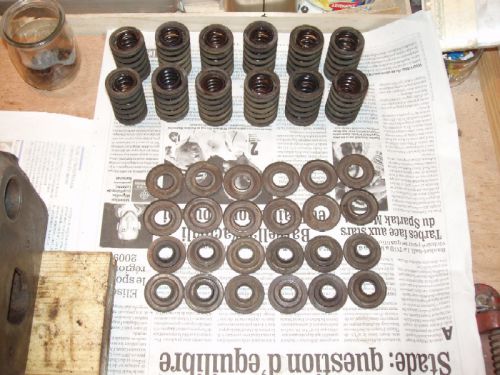
Une fois le remontage terminé, bien huiler l'ensemble pour éviter le retour de la corrosion.
Les culbuteurs (identiques à ceux des 4 cylindres) sont vérifiés et ceux qui ont trop de jeu sont éliminés au profit d'exemplaires à la bonne côte.
L'axe neuf est monté, joints neufs sous les colonnettes et arrêtoirs neufs.
Les écrous de rampe sont serrés au couple.

Culbuteurs bien alignés, comme pour la parade
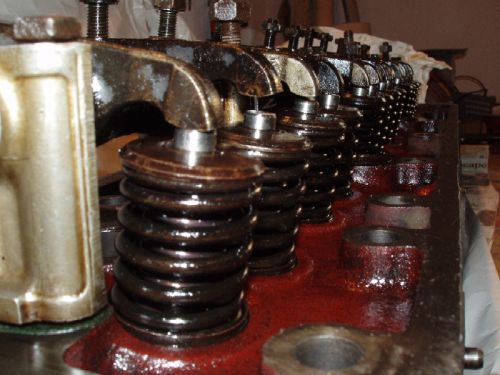
Il est temps de ranger soigneusement notre culasse rénovée, puis de passer à la suite des opérations...
On va s'intéresser maintenant aux bielles:
Les bielles d'origine, régulées, sont écartées au profit de bielles d'ID.
Celles-ci ont l'important avantage de permettre le montage de coussinets minces, moins onéreux qu'un régulage difficile pour lequel les artisans capables sont rares.
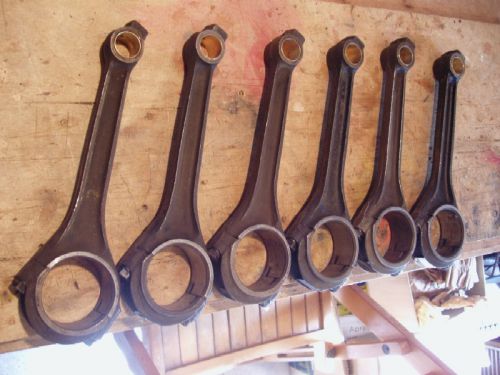
Elles sont équilibrées en poids, équerrées et leur pied est re-bagué et alésé à la côte des axes neufs de pistons par un atelier professionnel. Ce travail est hors de portée de l'amateur...
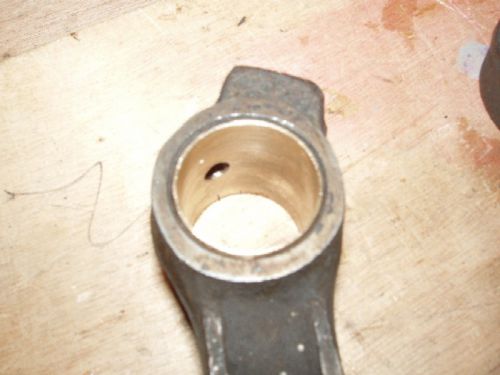
Une fois les bielles rénovées, il est grand temps de s'occuper du vilebrequin.
Il subit en préambule un nettoyage poussé EN PARTICULIER dans les conduits d'huile internes.
Ensuite, il est confié à un professionnel qui jugera la côte de rectification à lui donner.
Il faut lui fournir les coussinets d'arbre, commandés en fonction de la côte déterminée, et ceux de bielles pour faire un travail correct.
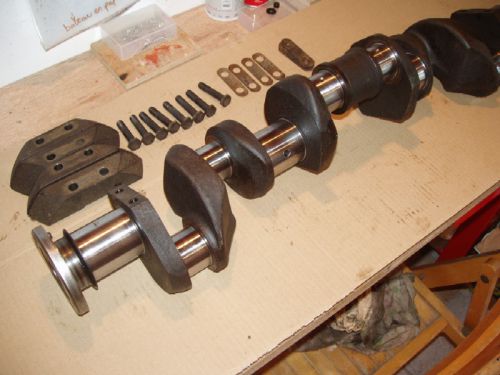
C'est une magnifique pièce qu'on récupère "un certain temps" plus tard...
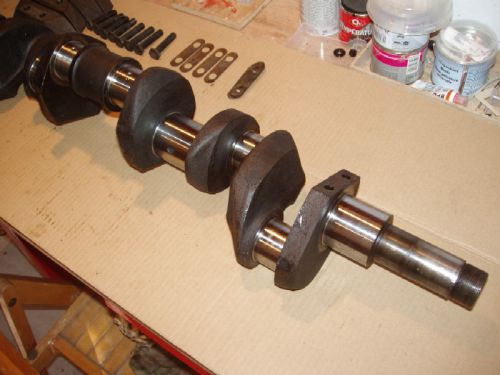
C'est également la pièce mobile la plus lourde (26Kgs) qu'on puisse trouver sur un moteur de Traction...
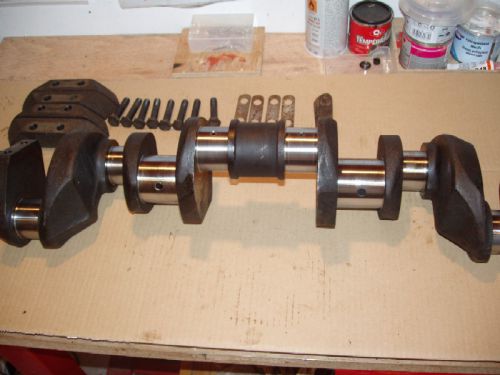
On ne s'attendrit pas trop quand même, et on en profite pour penser à changer le roulement pilote d'arbre primaire de boite à vitesses à l'avant du vilebrequin.
On remonte également les masses d'équilibrages soigneusement repérées au démontage.
On vérifie encore une fois, bielles montées, le bon équerrage de celles-ci: Pas le moindre vrillage ni flambage, c'est parfait, l'ajusteur a bien travaillé.
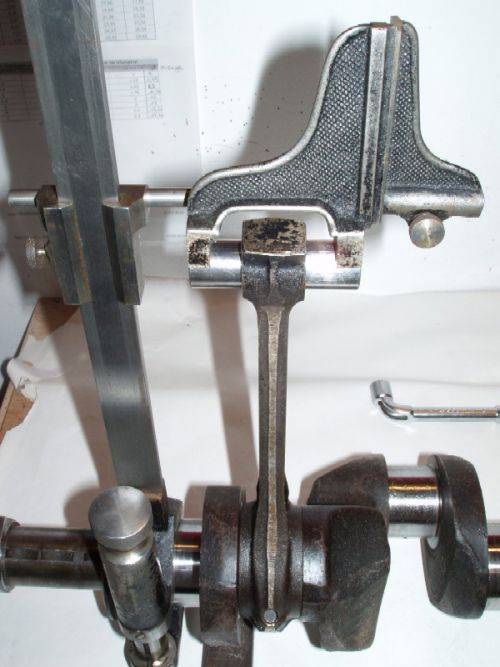
C'est fini pour le vilebrequin qu'on range soigneusement (bien protégé de la corrosion par une fine couche de graisse).
L'arbre à cames est irrécupérable, trop oxydé. Cette pièce n'existe pas en refabrication, il faut donc se mettre en quête d'un arbre d'occasion, en bon état.
Divers avis de professionnels convergent pour attester que l'acier utilisé pour les arbres à cames de traction avant est sensible à la corrosion.
Au premier plan, l'ancien arbre, au second celui qui sera retenu pour le montage.
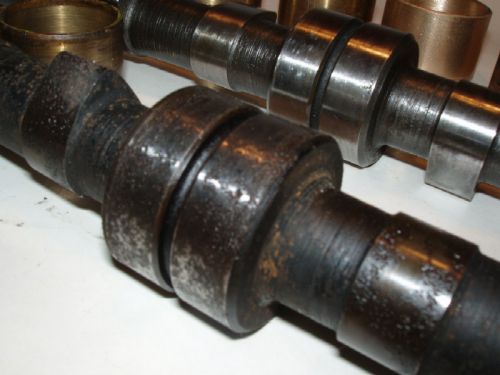
Sur certaines cames, c'est encore plus effrayant:
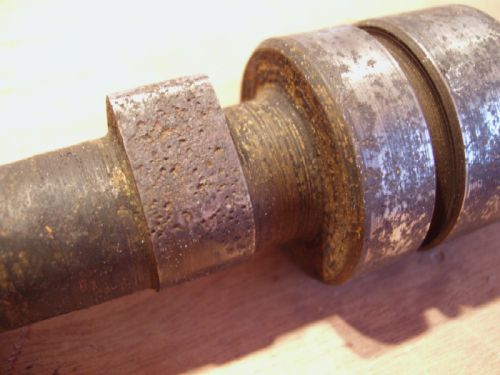
Occupons nous maintenant du bloc...
Pour le nettoyage, plusieurs litres d'essence seront nos alliés afin de venir à bout de 60 ans de cambouis et crasses divers.
C'est un gros travail, très salissant et rebutant.
On finit au nettoyant pour freins en bombe, en particulier dans les conduits d'huile pour bien les décaper.
Ensuite, de longs moments au nettoyeur à haute pression finiront les détails oubliés dans la première phase.
On obtient un bloc tout propre:
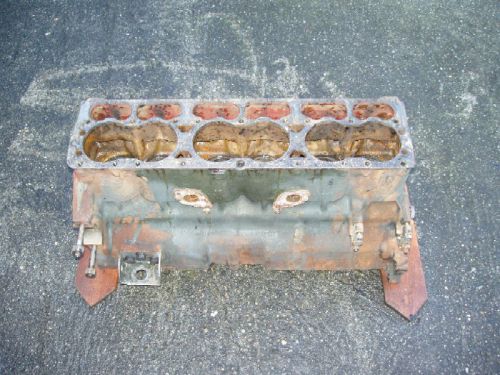
Mais on n'est pas au bout de nos peines, et le travail à faire sur le bloc est encore conséquent:
- Inspection très attentive dans tous les recoins afin de vérifier l'absence de cassures ou de criques
- Vérification de tous les filetages, en particulier ceux des goujons de culasse
- Grattage des chambres d'eau afin de détacher toutes les particules de rouille non adhérentes
- Ebavurage des conduits d'eau. En effet ceux ci présentent des bavures de fonderie restreignant le passage d'eau de manière évidente.
(Comment ça, elle chauffe la 15/6 ?)
Avant ébavurage:

Après: On a gagné facilement environ 15% de la section de passage
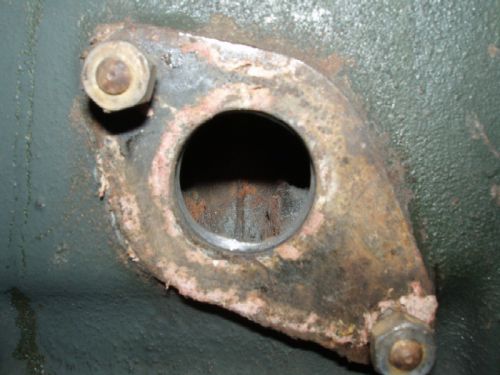
Egalement, contrôler scrupuleusement les surfaces d'appui des chemises dans le bloc qui doivent être parfaites. Aucun compromis n'est tolérable à cet endroit:
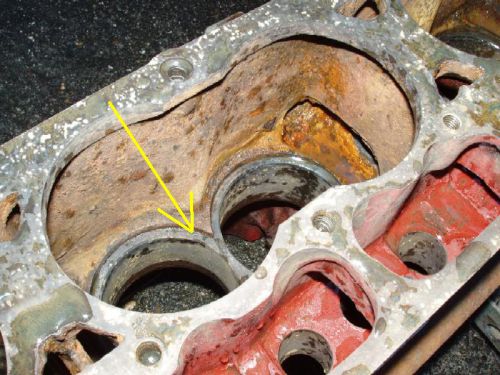
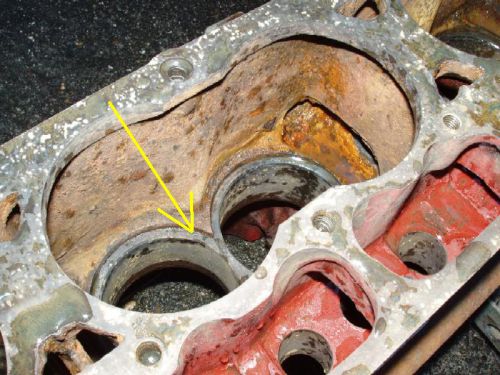
Les chambres d'eau sont alors traitées contre la rouille à l'aide d'un produit dérouillant, à base époxy pour résister à la chaleur:
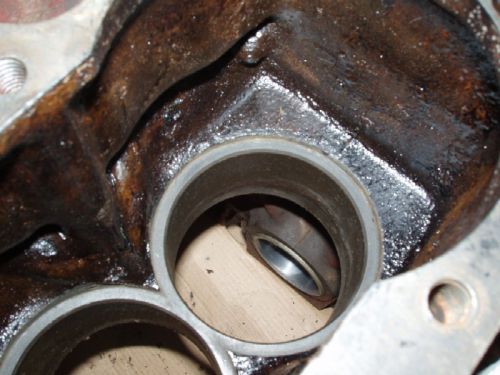
Mais ce n'est toujours pas fini, et il reste à faire un travail capital sur le bloc: Le changement des bagues d'arbre à cames.
Ces bagues sont en effet usées, et surtout ovalisées, remonter le moteur ainsi serait une erreur majeure: perte de pression d'huile, impossibilité de respecter la tension de la chaine de distribution, et certainement un bruit important de fonctionnement de l'arbre à cames.
Sur la photo d'une bague démontée, on aperçoit bien les traces d'usure et d'ovalisation sur les portées.
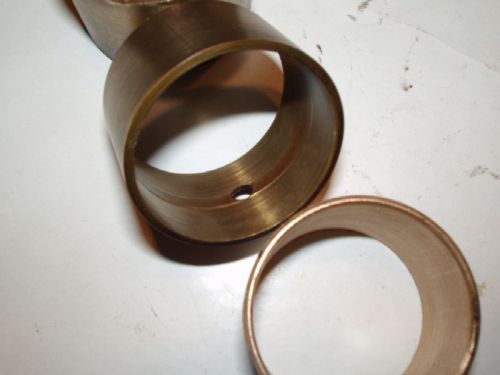
Le bloc prend donc le chemin (bien connu maintenant) de l'atelier spécialisé, et on le récupère re-bagué à neuf, avec un jeu correct au niveau des paliers:
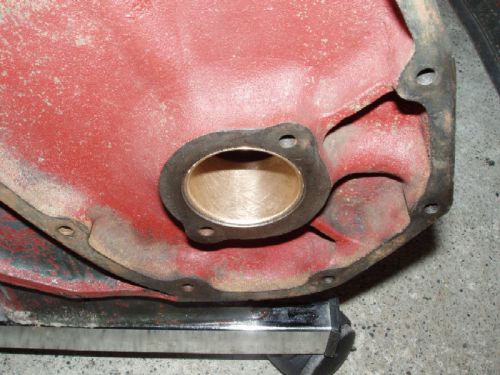
On est sûr du fonctionnement futur, l'ajustage étant fait à l'aide de l'arbre à cames qui sera monté sur ce moteur, bref du véritable sur-mesure !
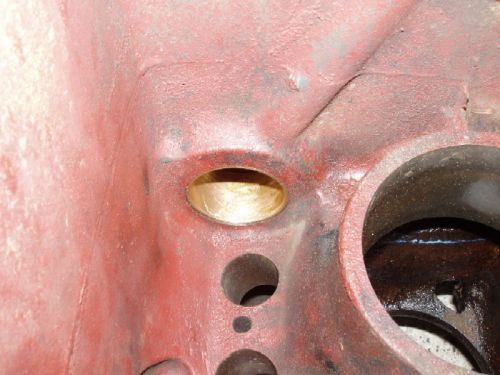
Une fois tout cela terminé, on s'aperçoit qu'approche enfin l'heure du remontage !
Le "point bas" de la restauration du moteur est atteint, la sous traitance spécialisée est finie et tout ce qui va suivre va nous rapprocher du moteur terminé.
Il est temps de placer nos coussinets neufs dans le bloc: un premier serrage léger pour que tout se mette bien à sa place:
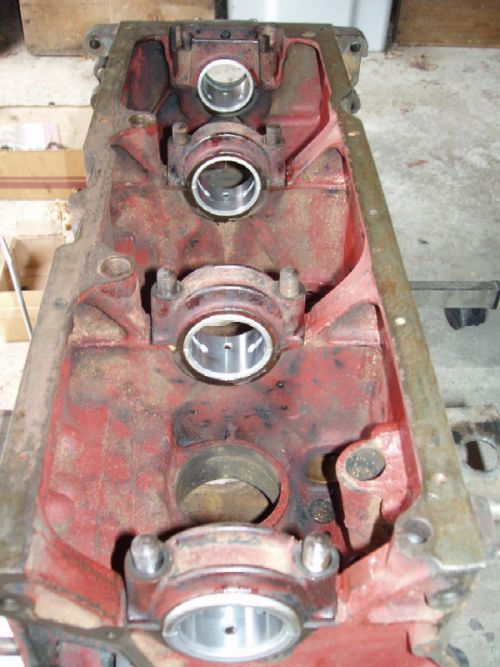
Et on re-démonte pour reposer le vilebrequin dans ses coussinets...moment émouvant:
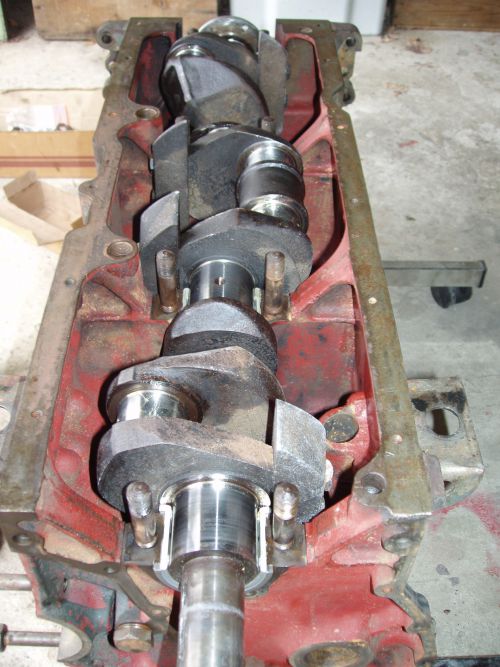
On remonte les chapeaux de paliers, on les serre au couple et on vérifie la bonne rotation de l'ensemble, sans jeu ni point dur. Dans ce cas précis, l'aléseur a fait du beau travail, le résultat est impeccable.
Il est alors temps de procéder à une opération primordiale pour la bonne tenue de la ligne d'arbre dans le temps, et son silence de fonctionnement: le réglage du jeu latéral du vilebrequin:
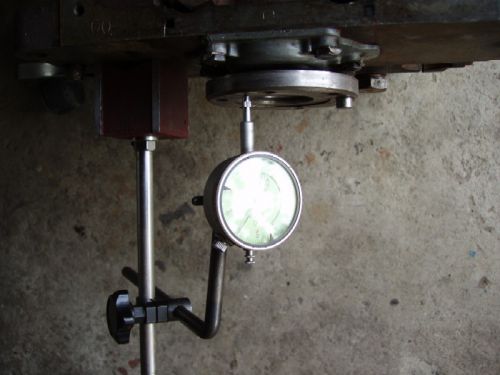
Il se règle à l'aide de cales placées coté distribution, et pour sa mesure précise un comparateur est bien préférable à un simple jeu de cales.
Le constructeur donne une fourchette entre 15 et 20 centièmes.
Mais auparavant, une intervention a été nécessaire: la rondelle d'appui du vilebrequin sur le palier (à gauche sur la photo) est trop marquée pour être remontée ainsi. Un changement par une neuve s'impose.
C'est indispensable: remonter la vieille rondelle à l'appui détérioré entrainera une usure accélérée du palier et une prise de jeu importante et hors tolérances, induisant rapidement une usure de la ligne d'arbre et ruinant le travail de remise à neuf.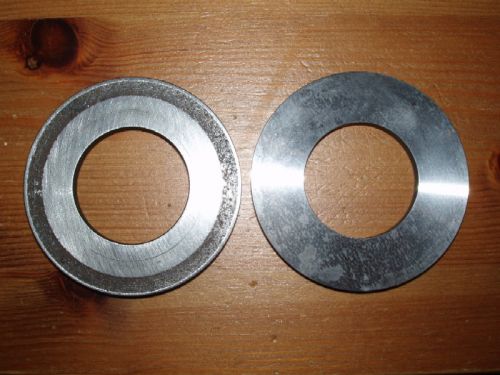
Il faut également, juste avant de régler le jeu, procéder au centrage des deux demi coussinets arrières: Monter la rondelle d'appui, sans cales de réglage, desserrer le chapeau de palier, puis serrer légèrement l'écrou de vilebrequin pour plaquer les deux demi coussinets sur la rondelle, ce qui réalise leur alignement parfait. Resserrer alors le chapeau de palier au couple.
Sur notre moteur, nous obtenons finalement un jeu de 16 centièmes, parfaitement dans les tolérances.
Il est temps maintenant de remonter l'arbre à cames.
On le place, bien huilé dans ses paliers, puis on pose la bride et on serre les vis au couple en ayant soin d'interposer deux arrêtoirs neufs.
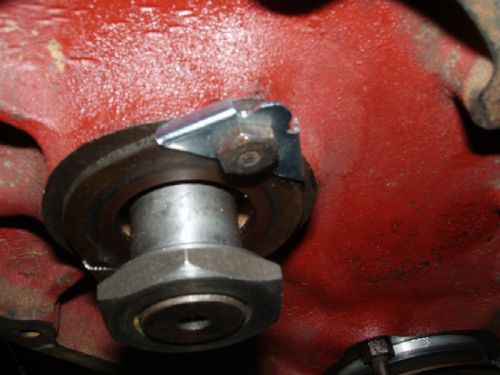
Si la bride est trop usée, sur la portée du pignon, monter une bride neuve, mais attention à sa qualité (voir l'article : "les pièces neuves à jeter")
Il est temps maintenant de remonter la commande de la distribution, soit la chaine et ses deux pignons.
Ici, tout est neuf, c'est plus simple. Il est très peu recommandé de panacher à ce niveau des pièces neuves et des pièces anciennes, traditionnellement, l'ensemble se change.
Il faut d'abord aligner les deux pignons, recouverts de la chaine selon les prescriptions du constructeur. La photo parle d'elle même:
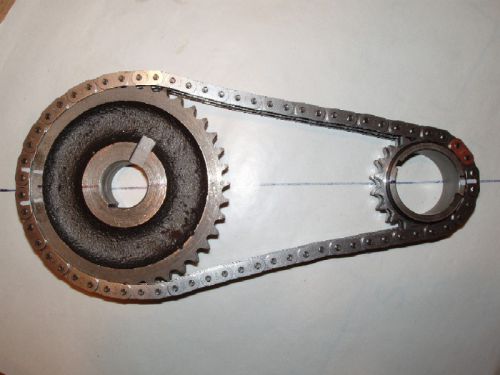
Une droite doit passer par les centres des pignons et les repères de ceux-ci, placés à l'intérieur des pignons.

Le pignon d'arbre à cames est toujours repéré sur une dent.
Le pignon de vilebrequin est repéré soit sur un entre-dent (comme sur la photo), soit sur une dent.
Dans ce dernier cas, le repère sera décalé à droite de la ligne (soit l'équivalent du dessus sur la photo).
Afin de ne pas se tromper, ni décaler au montage, il est recommandé de rajouter des repères en périphérie des pignons et de la chaine (visibles également sur la 1° photo). On est ainsi bien certain de monter l'ensemble correctement.
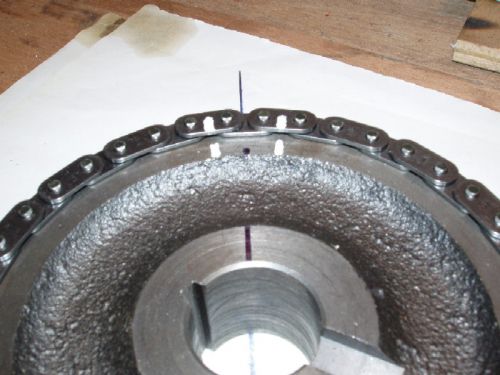
Le pignon de vilebrequin est repéré soit sur un entre-dent (comme sur la photo), soit sur une dent.
Dans ce dernier cas, le repère sera décalé à droite de la ligne (soit l'équivalent du dessus sur la photo).
Afin de ne pas se tromper, ni décaler au montage, il est recommandé de rajouter des repères en périphérie des pignons et de la chaine (visibles également sur la 1° photo). On est ainsi bien certain de monter l'ensemble correctement.
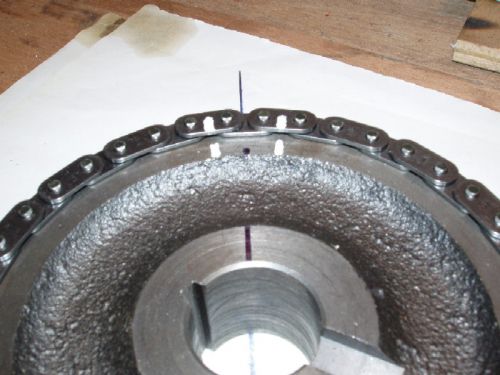
Bien, maintenant que notre ensemble chaine/pignons est bien aligné, comment le monter sur le moteur ?
Rien de bien compliqué: commencer par aligner le vilebrequin avec les deux cylindres extrêmes au P.M.H. (point mort haut): Cela correspond justement à une position de la clavette de vilebrequin vers le haut.
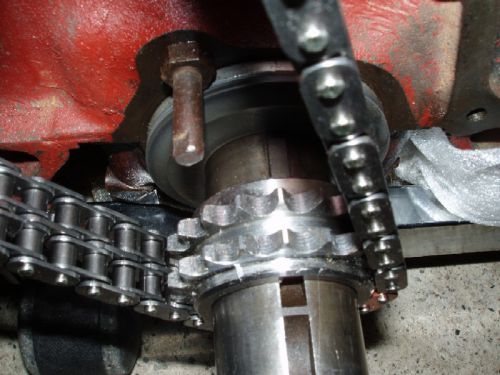
Pour l'arbre à cames, la clavette sera horizontale et dirigée vers la gauche du moteur.
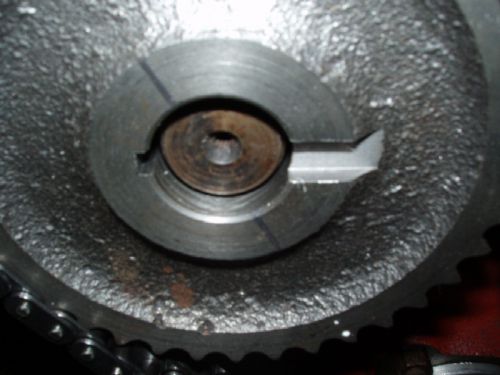
Engager alors doucement l'ensemble chaines/pignons en place, sans faire sauter la chaine. Les repères faits en périphérie des pignons sont utiles pour vérifier qu'on ne se décale pas au montage.
Tourner légèrement l'arbre à cames si nécessaire pour permettre la bonne introduction des pignons bien à fond sur leurs portées. Leur mise en place se fait très progressivement et alternativement, afin de ne pas tordre la chaine et la contraindre. Vérifier que les clavettes sont bien engagées dans les rainures et ne sortent pas de leurs logements.
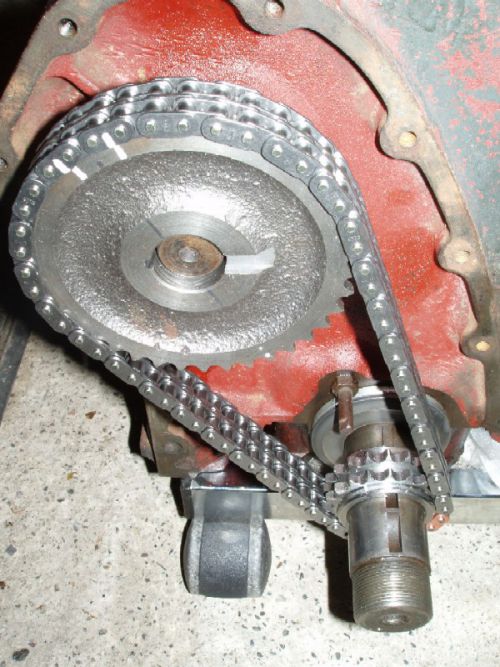
Vérifier encore le bon alignement des repères puis tourner le vilebrequin de plusieurs tours dans un sens puis l'autre. On doit revenir sans souci sur le calage originel.
Placer alors l'arrêtoir d'écrou sur l'arbre à cames, l'écrou et serrer au couple.
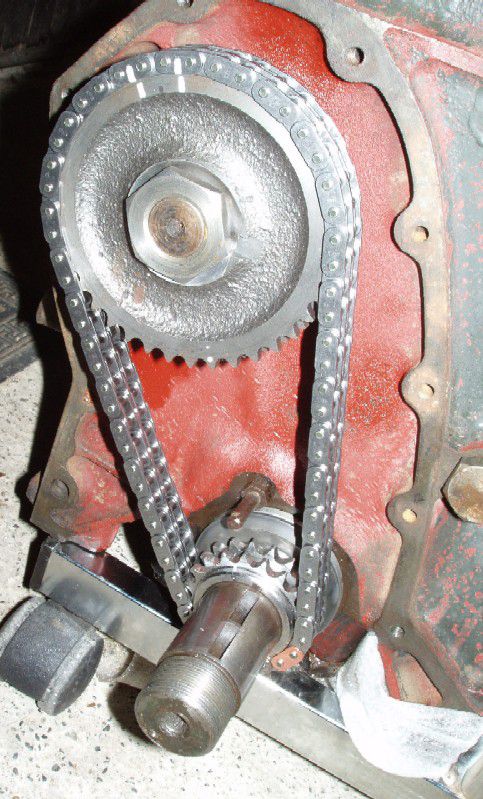
Dernière étape: rabattre l'arrêtoir d'écrou:
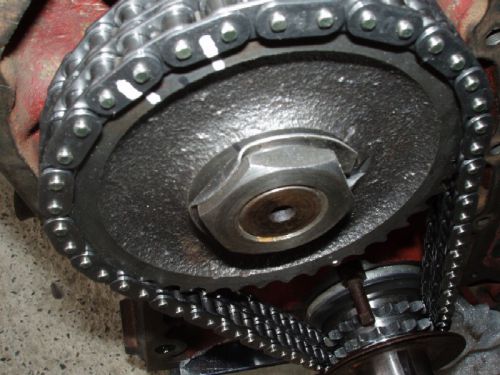
La distribution est alors en place et correctement calée.
Il est temps de cacher tout cela sous le carter de distribution, mais non sans avoir replacé les deux clavettes de vilebrequin, après il sera trop tard pour l'une d'entre elles.
Le carter est prêt, avec son joint neuf que l'on va "enrichir" avec la célèbre pâte HERMETIC. Cette pâte à joints, aussi vieille que la Traction se trouve chez les bons revendeurs de pièces détachées ou encore chez les Shipchandlers.
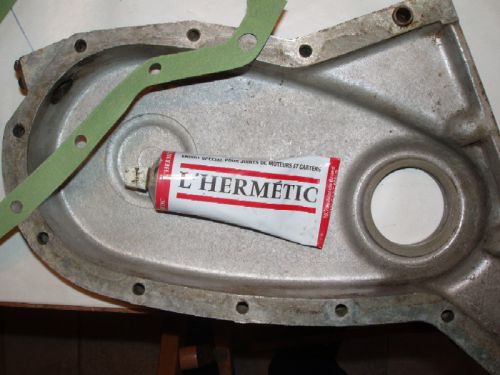
Une fois le joint enduit sur ses deux faces, voilà le résultat: le carter est prêt à la pose.

Placer le carter qui se centre seul grâce à ses deux pieds de centrage, puis l'ensemble des vis et serrer au couple.
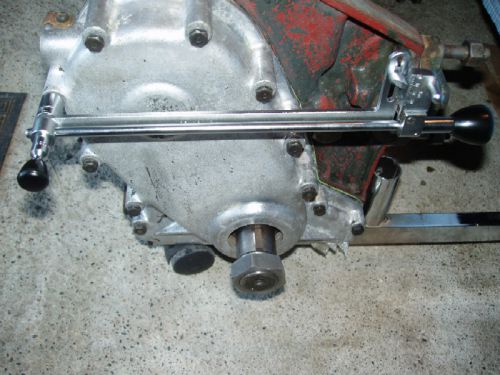
C'est terminé de ce coté, vérifier une dernière fois qu'on n'a pas oublié de placer les clavettes de vilebrequin, sinon il faut recommencer. La distribution est cachée pour longtemps.
On remarque que l'écrou crênelé de vilebrequin d'origine n'est pas réutilisé, c'est une refabrication en 6 pans, bien plus pratique qui sera montée sur ce moteur (voir l'article des bonnes adresses).
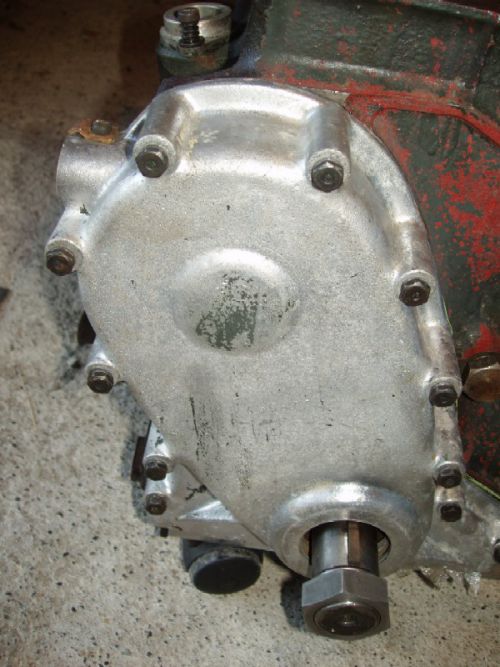
Il est temps de passer à l'avant de l'arbre à cames. Le carter de sortie coté poulie est préparé de la même manière que l'arrière.
Sur la sortie d'arbre, on place la rondelle déflectrice d'huile, puis la clavette.
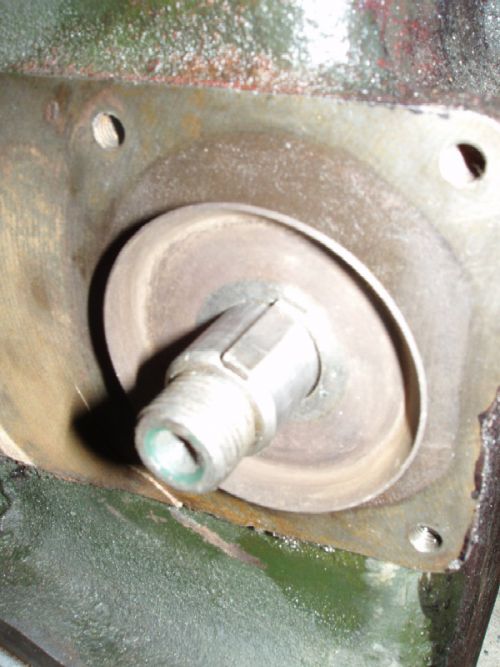
On remarque que l'écrou crênelé de vilebrequin d'origine n'est pas réutilisé, c'est une refabrication en 6 pans, bien plus pratique qui sera montée sur ce moteur (voir l'article des bonnes adresses).
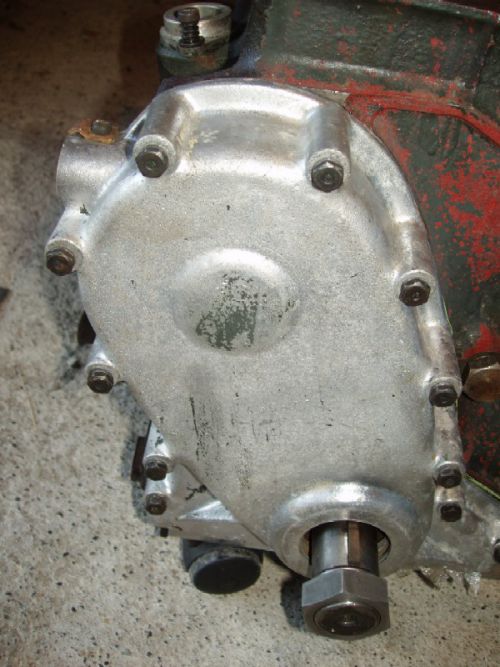
Il est temps de passer à l'avant de l'arbre à cames. Le carter de sortie coté poulie est préparé de la même manière que l'arrière.
Sur la sortie d'arbre, on place la rondelle déflectrice d'huile, puis la clavette.
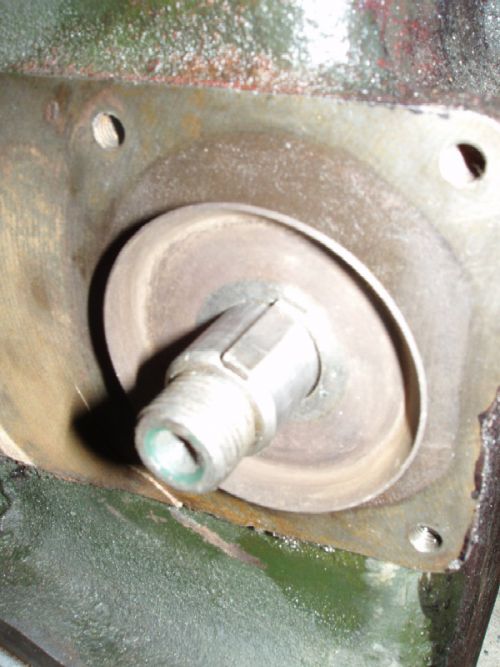
Ensuite, placer la coquille/carter, approcher les 4 vis de fixation et la centrer.
Ici, pour le centrage, il est utilisé un vieux moyeu d'une poulie cassée.
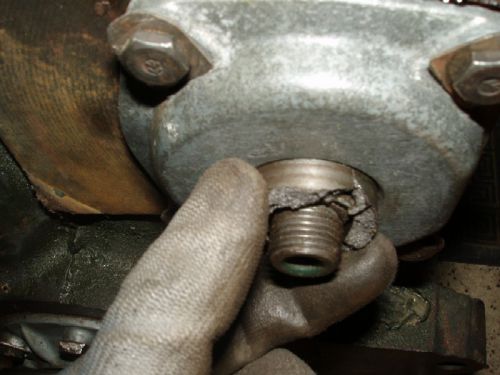
C'est d'une inélégance totale, mais c'est finalement efficace et précis, car le moyeu de poulie ne doit frotter en aucun endroit de la coquille, munie de filets de retour d'huile qui ne doivent jamais être en contact avec la partie tournante, ce qui les déteriorerait irrémédiablement.
Une fois le centrage correctement réalisé, finir le serrage au couple et rabattre les arrêtoirs.
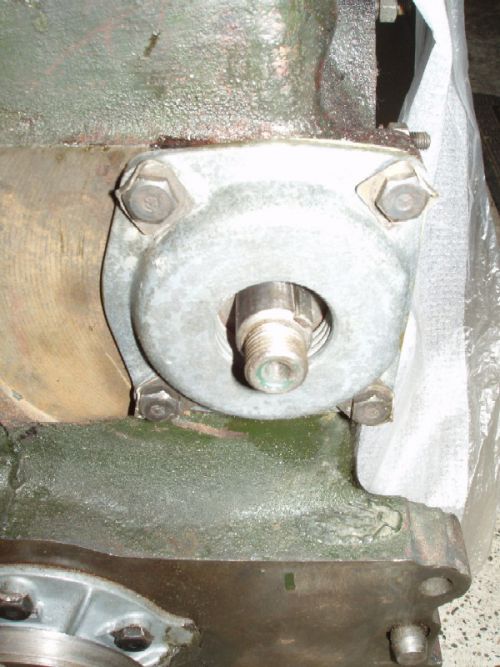
Il est temps maintenant de monter les ensembles chemises, pistons bielles.
Les bielles, et ensembles pistons/chemises neufs ont été soigneusement repérés préalablement pour ne pas être désappariés.
Pour mémoire, on contrôle d'abord le jeu à la coupe des segments, qui doit correspondre aux indications du fabricant (différentes de celles du constructeur à l'époque).
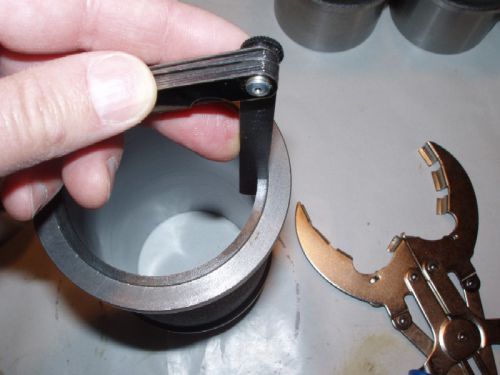
Nous préférons nettement la méthode consistant à monter la bielle sur le piston, le piston dans la chemise, et l'ensemble dans le moteur: en effet, l'engagement du piston par le bas de la chemise, munie d'un chanfrein à cet endroit, est nettement moins dangereux pour la casse d'un segment que par le haut, même avec un bon collier à segments.
La tête de bielle passera facilement par l'embase de la chemise dans le bloc à condition de déposer le chapeau.
Commençons donc par monter les bielles sur les pistons.
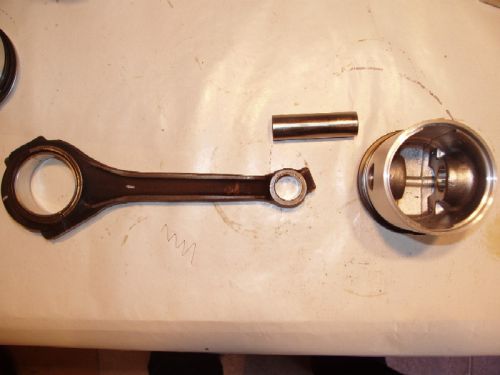
La pose des circlips d'arrêt d'axe de pistons doit se faire en orientant la coupe de manière à ce que le mouvement vertical du piston n'ait pas tendance à l'ouvrir, ni à le faire tourner dans sa gorge:
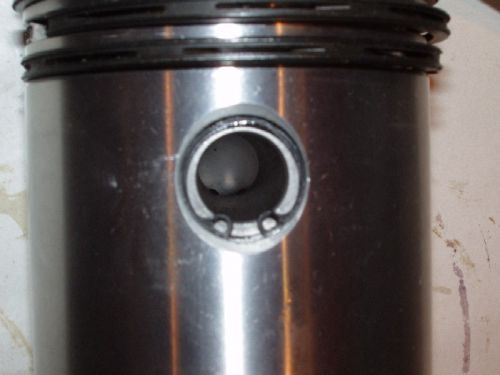
L'axe s'introduit "au pouce" (même si on peut tricher en utilisant l'index, il n'y aura aucune conséquence sur la marche du moteur).
Poser ensuite le deuxième circlips.
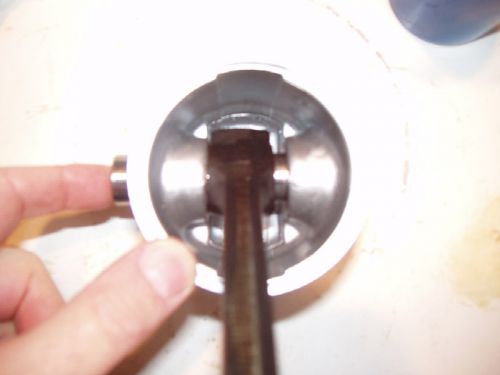
ATTENTION, lors de cette opération d'orienter correctement le piston par rapport aux repères de la bielle pour son montage futur dans le moteur.
S'il est repéré sur sa tête d'une flèche constituée de petits points, elle doit être orientée vers l'arbre à cames.
Si la flèche est constituée de petits tirets, c'est vers l'avant du moteur (coté volant).
On ne peut confondre l'un et l'autre du fait de la position de l'axe, bien évidemment, mais on peut monter le piston à l'envers !
ATTENTION également, si l'on utilise des bielles ID DS ou 11D: La coupe de ces bielles doit impérativement être orientée coté arbre à cames.
Bien vérifier tout cela au cours du montage.
Une fois cette opération répétée 6 fois, on doit obtenir ce genre de chose:
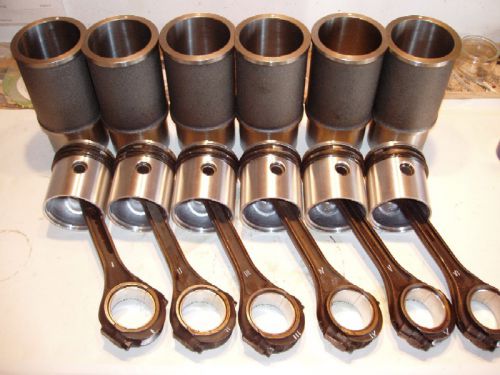
Insistons encore une fois sur l'importance d'un bon repérage de l'ensemble des pièces, seul garant d'un montage correct et facile. Une fois le moteur refermé, il sera bien trop tard...
Prendre garde, lors du repérage, que les méplats des chemises sont alternativement vers l'avant et l'arrière du moteur.
Idéalement, repérer les chemises/pistons neufs par numéros 1-2-3-4-5-6 puis placer les chemises comme on les montera dans le moteur, et repérer le coté arbre à cames (un point blanc par ex) ce qui permettra l'orientation correcte du piston au moment de l'appariement chemise/piston-bielle.
Bien, arrachons nous à la contemplation de ce bel ensemble et passons à la phase suivante: le montage des pistons/bielles dans les chemises.
Auparavant, il faut vérifier le dépassement des chemises du bloc.
Les ensembles modernes sont usinés aux spécifications "11D", c'est à dire qu'il n'y a normalement pas de réglage à faire: La chemise est à une côte de dépassement zéro, et le seul montage du joint papier suffit à assurer la bonne hauteur de dépassement.
On vérifie, et effectivement, montée sans joint la chemise arase juste le bloc:
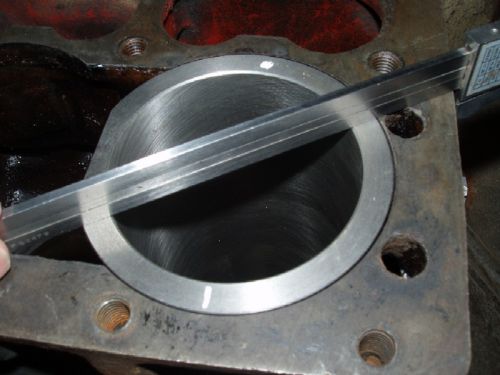
On en profite pour contrôler cela sur chacun des cylindres, et en plusieurs points pour s'assurer du bon état des différentes embases de chemises.
Le joint papier mesure 7 centièmes d'épaisseur, ce qui convient parfaitement pour un dépassement raisonnable.
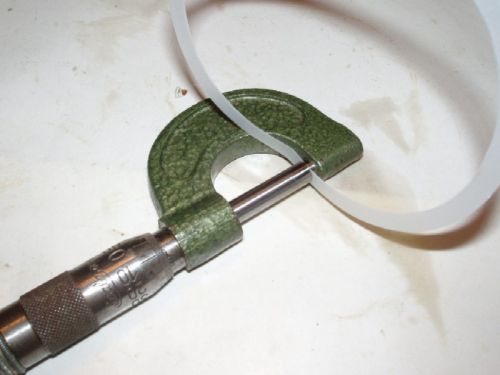
Montage des pistons:

Auparavant, il faut tiercer les segments. Ici, ils sont au nombre de quatre, on va donc les "quarter" ...
On les oriente à 180° l'un de l'autre, légèrement décalés par rapport à l'axe du piston:
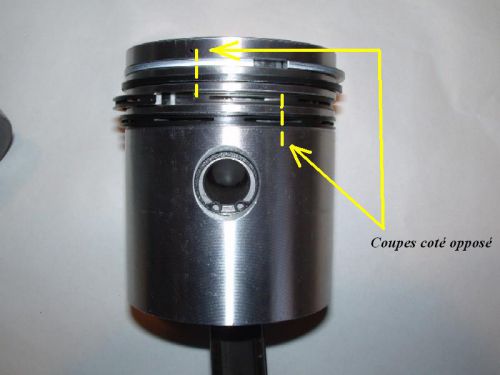
Huiler abondamment la chemise et le piston, après avoir éliminé la cire de protection d'origine.
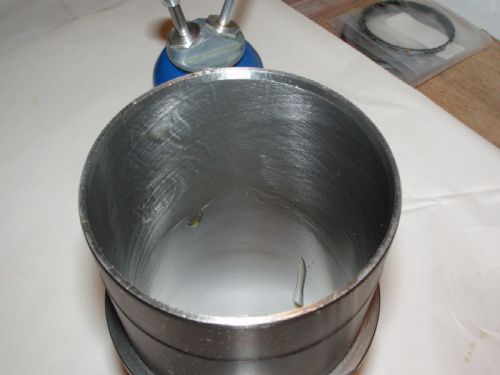
Monter le piston huilé dans un collier à segments. Il est aventureux de se passer de cet outil pour un emmanchement sans risque de casse:

Et il ne reste plus qu'à terminer l'introduction du piston dans sa chemise, en PRENANT GARDE à respecter l'orientation de l'ensemble par rapport à la position future de la chemise en regard de l'arbre à cames.
En procédant à une introduction par le bas, c'est très facile: une poussée sur la bielle suffit pour que tout rentre souplement et sans frapper du fait de l'embase évasée de la chemise. C'est nettement plus sûr que par le haut:
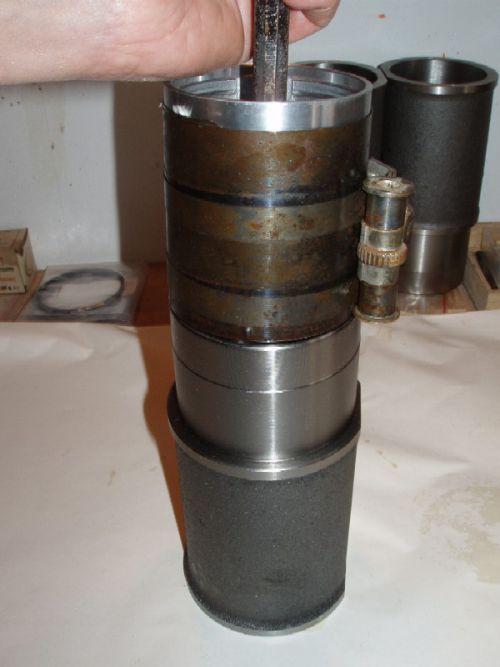
Il est maintenant temps de placer nos ensembles chemises/pistons/bielles dans le bloc.
Avant tout, traquer toute impureté sur les embases !
C'est très important, remonter la chemise sur une embase sale entraînera irrémédiablement des fuites
La préparation est simple, enlever le chapeau de tête de bielle (sinon, elle ne passe pas dans l'embase des chemises sur le bloc) puis mettre un peu d'Hermétic sur l'emplacement du joint.
Ce n'est pas absolument indispensable, mais pas contre indiqué non plus. Par principe, sur un moteur ancien, nous préférons en mettre toujours un peu.

Puis placer le joint en prenant garde de ne pas le déchirer:
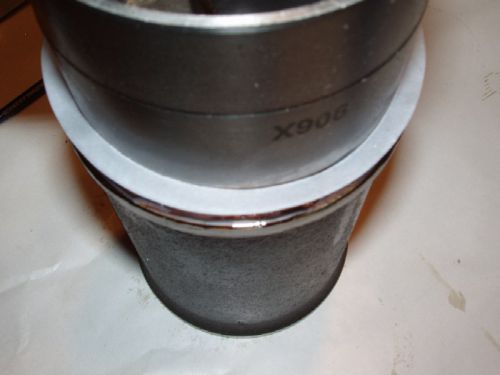
Et enfin, une dernière séance d'Hermétic:
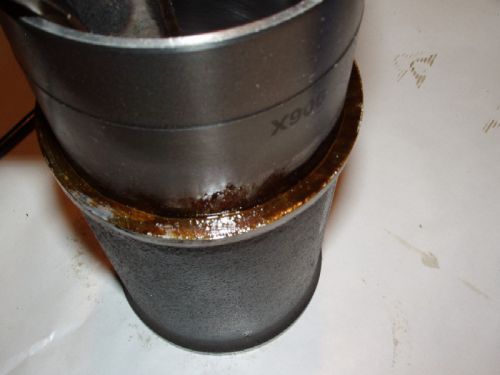
Puis huiler à la burette les paliers de bielle:
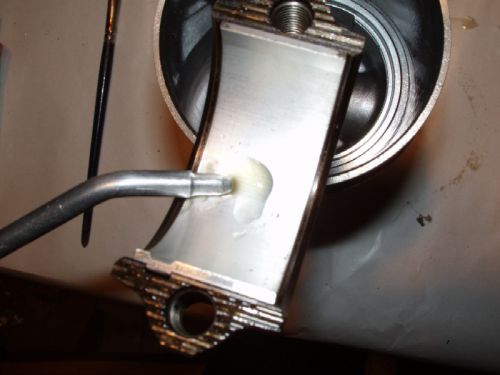
Il ne reste plus alors qu'à insérer la chemise dans le bloc, correctement orientée.
On ne regrette pas ici le temps passé à faire des repères sérieux et cohérents.
Attraper par en dessous la tête de bielle, placer le chapeau de palier dans le bon sens (repères !) et le serrer modérément. On fera le serrage au couple lorsque tous les paliers seront en place.
On monte les chemises par paires, puis elles doivent être immobilisées par des rondelles (par exemple) pour ne pas se décoller de leur embase lors de la rotation du moteur pour attacher les paliers de bielles.
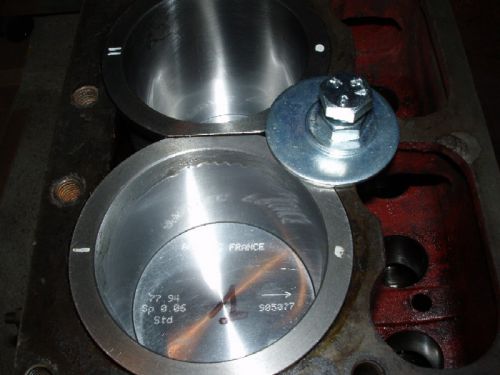
Au fur et à mesure du montage des ensembles, le moteur devient de plus en plus dur à tourner à la main. C'est normal.
On contrôle bien l'orientation correcte de chaque élément, et une fois de plus on se félicite d'avoir tout correctement repéré.
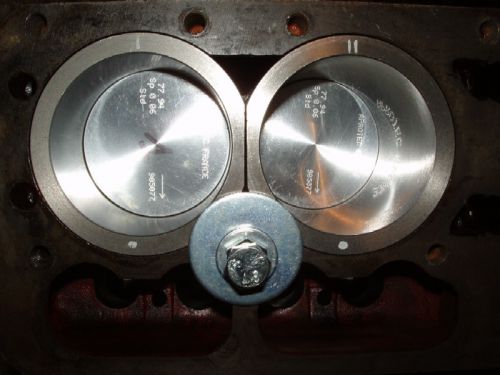
Profitons en pour vérifier la côte de dépassement des chemises au dessus du plan de joint du bloc.
Ici, la cale de 9 centièmes passe bien et la 10 passe gras. Cela se présente pas mal !
Contrôler cela dans plusieurs axes, mais ne pas oublier qu'on travaille sur un moteur ancien aux côtes parfois pas très justes. Ne pas traquer le centième mais vérifier la cohérence de l'ensemble.

Au bout du compte (jusqu'à six !) on doit obtenir cet objet :

Cela commence furieusement à ressembler à un moteur de 15/6 !
On s'amuse un moment à faire tourner tout ce bazar, histoire de voir le joli mouvement des pistons, mais on ne s'émeut pas trop, car il reste une opération capitale à exécuter, après avoir retourné le moteur:
Le serrage des chapeaux de bielles.
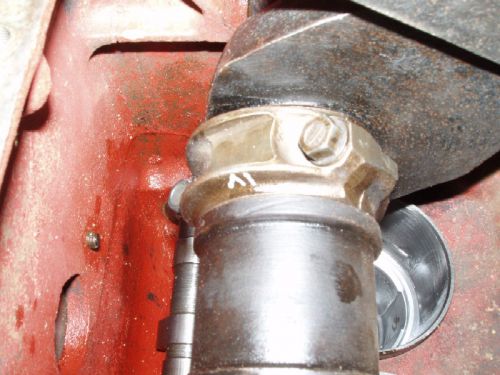
On vérifie une dernière fois la bonne orientation des coupes de bielles, des chapeaux, puis on procède bielle par bielle, en commençant par dégraisser très soigneusement chaque vis et son alésage:
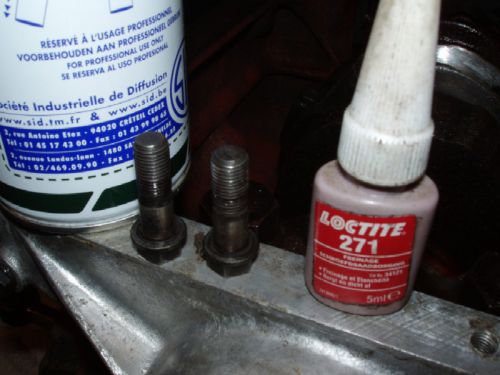
C'est une étape indispensable pour que le produit de freinage des filets fasse effet correctement.
Bien enduire les vis, puis les monter rapidement avant que le produit ne prenne et les serrer IMPERATIVEMENT à la bonne valeur de couple (5 m.kg pour les vis type 11D)
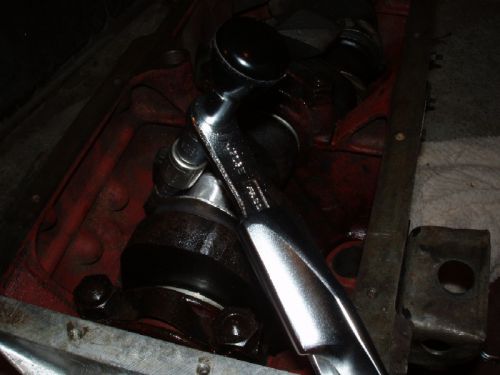

Cela commence furieusement à ressembler à un moteur de 15/6 !
On s'amuse un moment à faire tourner tout ce bazar, histoire de voir le joli mouvement des pistons, mais on ne s'émeut pas trop, car il reste une opération capitale à exécuter, après avoir retourné le moteur:
Le serrage des chapeaux de bielles.
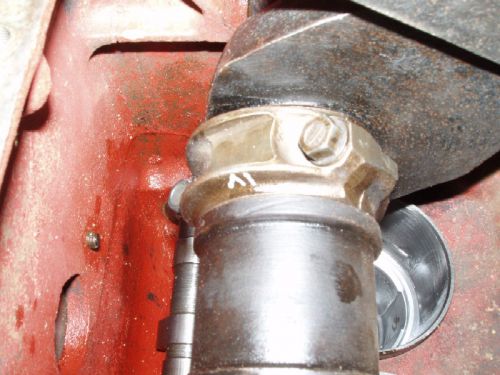
On vérifie une dernière fois la bonne orientation des coupes de bielles, des chapeaux, puis on procède bielle par bielle, en commençant par dégraisser très soigneusement chaque vis et son alésage:
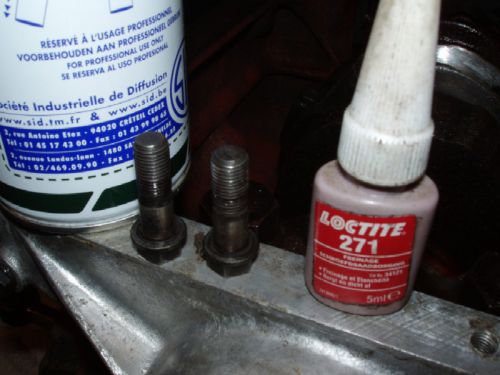
C'est une étape indispensable pour que le produit de freinage des filets fasse effet correctement.
Bien enduire les vis, puis les monter rapidement avant que le produit ne prenne et les serrer IMPERATIVEMENT à la bonne valeur de couple (5 m.kg pour les vis type 11D)
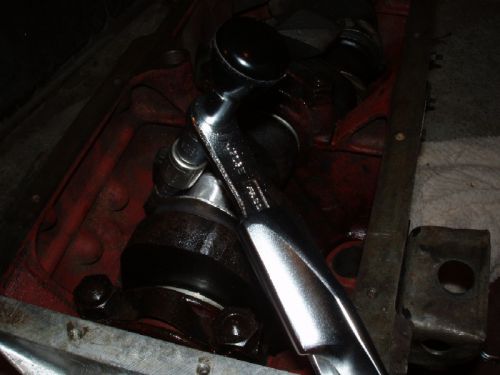
Voilà, il ne reste plus qu'à réaliser cette opération 6 fois et on a bel et bien notre bloc enfin prêt à recevoir sa culasse.
Prêt ? pas tout à fait puisqu'il manque les poussoirs.
Chacun, repéré au démontage, est soigneusement nettoyé et vérifié. Ici, les poussoirs d'origine sont encore à la bonne côte et n'ont pas de jeu dans leurs alésages. On les réutilisera donc:
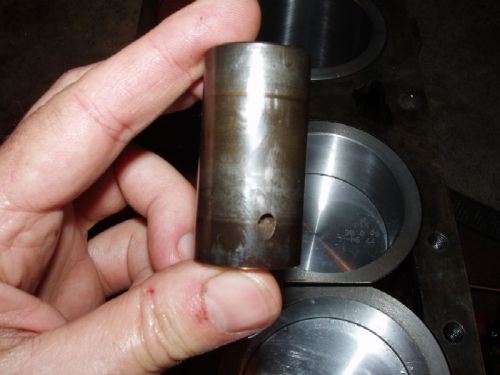
Huilage très abondant, et chacun réintègre son emplacement.
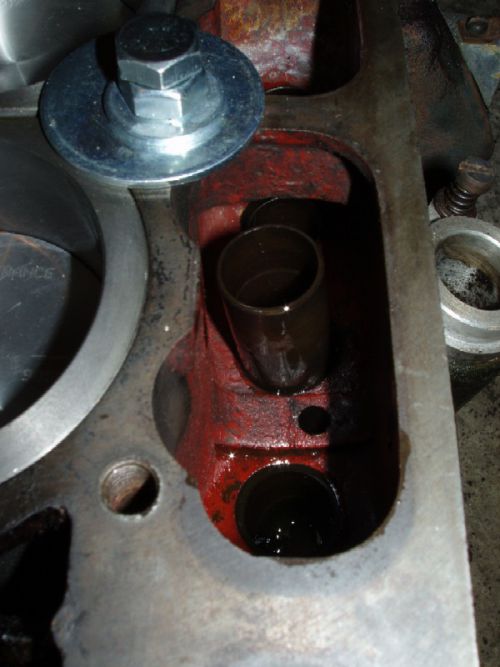
Une fois en place, on vérifie que les 12 coulissent bien librement.
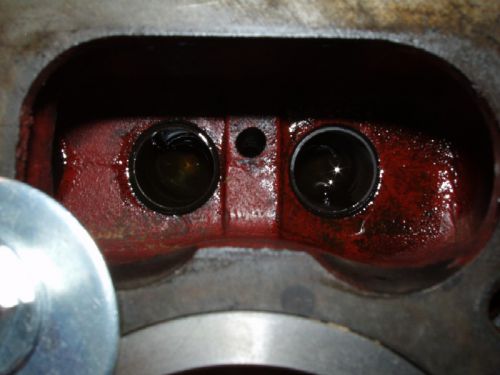
Vérification des goujons et écrous de fixation de la culasse. Si l'on réutilise ceux d'origine, s'assurer que les filetages sont impeccables et bien brossés.
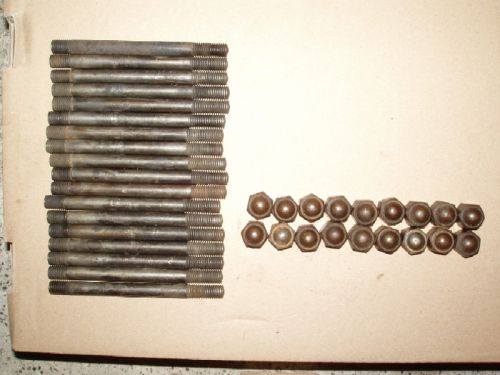
Nous sommes de nature méfiants avec les écrous borgnes pour le serrage des culasses.
Le risque existe que le serrage arrive à fond de filets avant que la culasse soit correctement serrée. Vérifions cela:
Un goujon est mis en place, petit filetage coté bloc, puis l'écrou serré à fond de filet. On vérifie la côte : 94 mm.
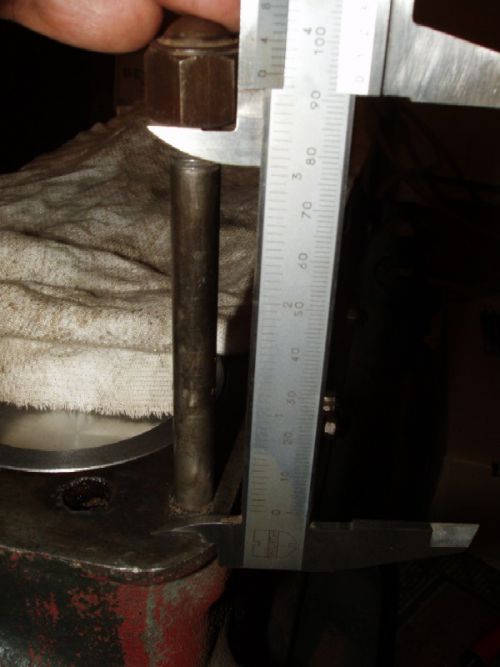
Aïe, c'est exactement la côte d'épaisseur de la culasse. Le joint, non comprimé, fait 2,2 mm et la rondelle d'origine sous l'écrou 1 mm.
Le constructeur a prévu bien juste à ce niveau: Par précaution, nous monterons des rondelles inox de 2 mm, soit un total de marge de 4,2 mm avant d'arriver en fond de serrage, ce qui correspond à un peu plus de 2,5 tours d'écrou.
Remontage des goujons sur le bloc:
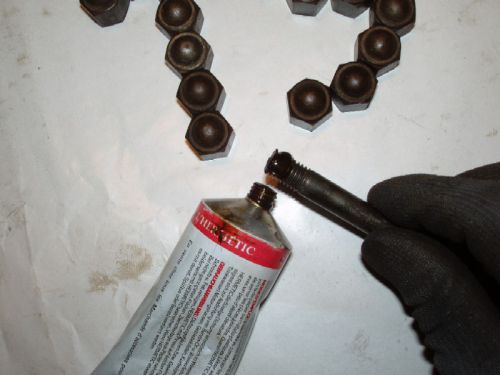
Le petit coté du filetage vient dans le bloc. On l'enduit d'un peu d'Hermétic, puis vissage et serrage au couple (2 m.Kg)
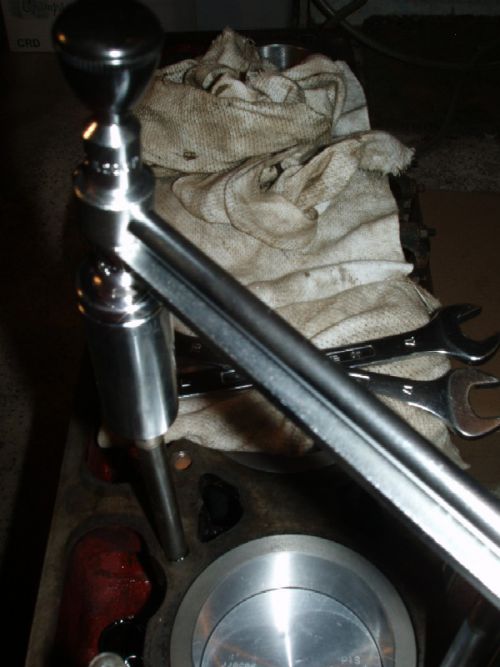
C'est assez long, avec la méthode écrou/contre-écrou, mais on avance la forêt de goujons.
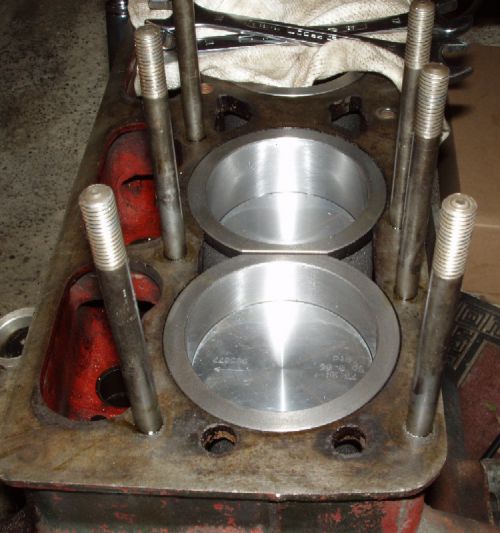
Passons au joint de culasse. Le montage se fera coté lisse vers le bloc et les sertissages vers la culasse.
On vérifie qu'il passe bien sur les goujons et le pied de centrage de la culasse.
On le monte enduit d'huile moteur: Le but est ainsi de favoriser le glissement du cuivre contre la fonte au moment de son écrasement par le serrage des goujons au couple, et d'éliminer toute contrainte sur les minces et donc fragiles pellicules de cuivre entourant la matière isolante du joint.
.
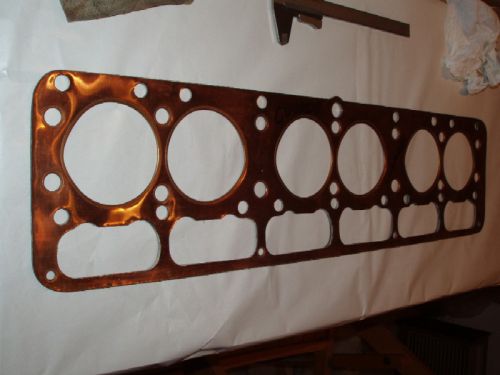
Une fois le joint posé dans le bon sens, placer la culasse, les 18 rondelles et écrous borgnes.
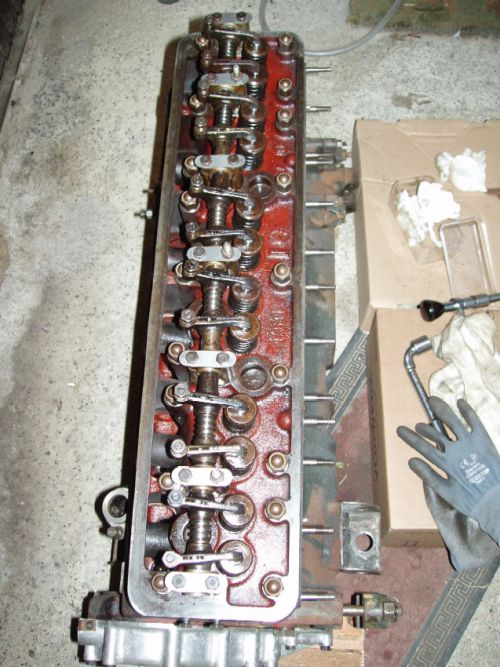
On obtient quelque chose qui ressemble de plus en plus à un moteur de 15/6.
Faire suivre par la séquence de serrage au couple, et dans l'ordre donné par le constructeur, des écrous.
1° serrage à 2 mKg, puis un deuxième à 5 mKg. Réaliser ces opérations très progressivement et en revenant sur le dernier serrage au moins deux fois.
Les filetages ont été préalablement huilés, ainsi que les faces d'appui des écrous.
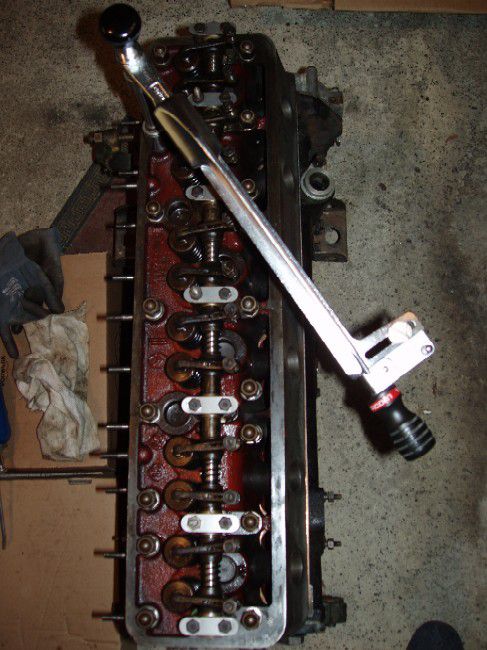
Nous utilisons des rondelles inox de 2mm d'épaisseur, comme indiqué plus haut, afin d'éviter le souci d'arriver à fond de filet avant le bon serrage.
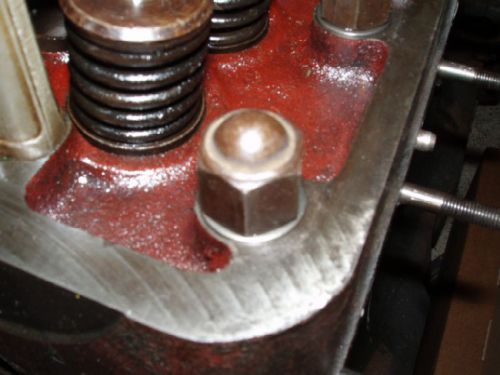
ADDITIF: On s'est un peu inquiété pour rien !
Il s'avère, suite à une info pêchée auprès d'un autre tractionniste passionné, que les écrous borgnes sont des "faux borgnes".
Le dôme de l'écrou n'est pas monobloc, mais est en fait un petit chapeau rapporté, qui saute facilement au serrage à fond de filet. Aucun risque donc, hormis de perdre le chapeau dans le bas moteur, d'avoir un serrage insuffisant. Merci Gérard pour la trouvaille, bien peu doivent savoir cette astuce. Cela n'empêche pas de monter des rondelles inox qui ne s'écrasent pas au serrage.
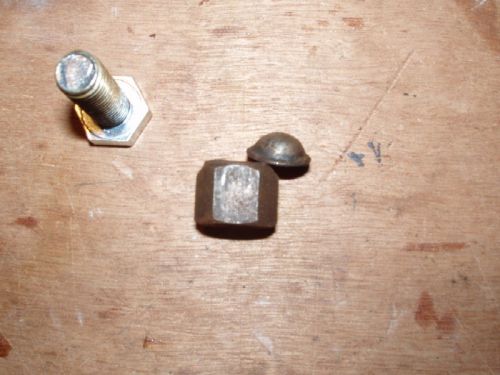
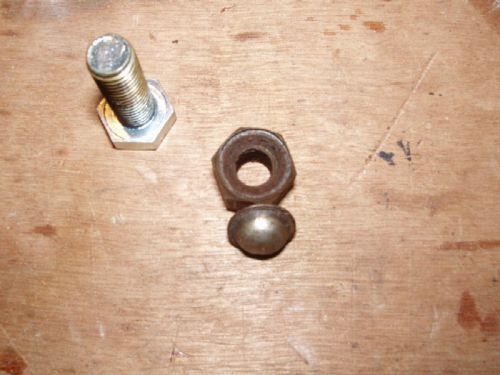
Replacer ensuite les tiges de culbuteurs, repérées au démontage avec une bonne goutte d'huile dans les rotules.
Elles passent très facilement en dévissant à fond les vis des basculeurs.
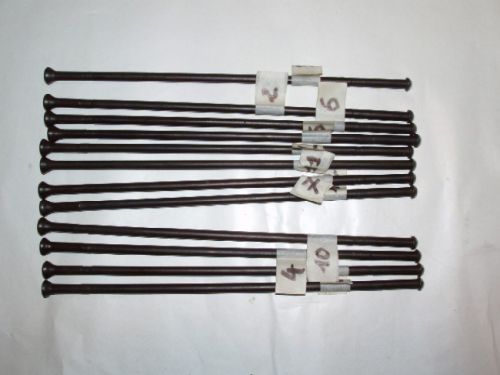
On peut alors réaliser un premier réglage de culbuteurs (voir article correspondant pour les détails). Inutile d'y apporter une précision importante, il faudra le refaire après resserrage de la culasse.
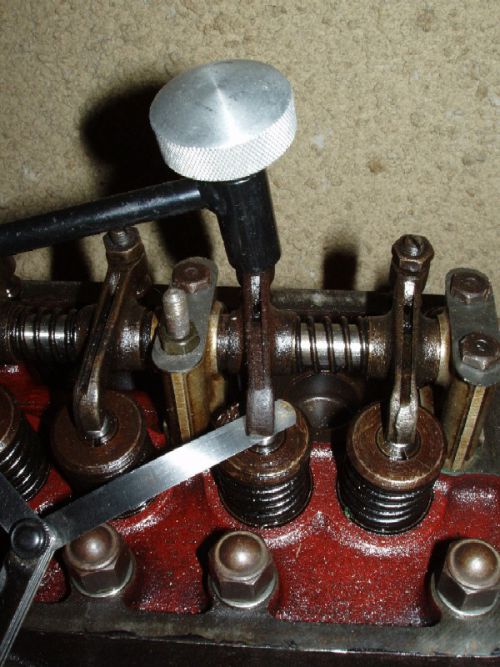
Bon, en haut du moteur, ça commence à être bon, il est temps de passer à la partie basse où le remontage de la pompe à huile reste à faire.
Préalablement, nous allons la tarer, et surtout vérifier son bon fonctionnement avec un montage très proche de celui décrit dans le M.R. (manuel des réparations) du constructeur.
(Encore merci à Julien et Jean Christophe pour le prêt du banc d'essais)
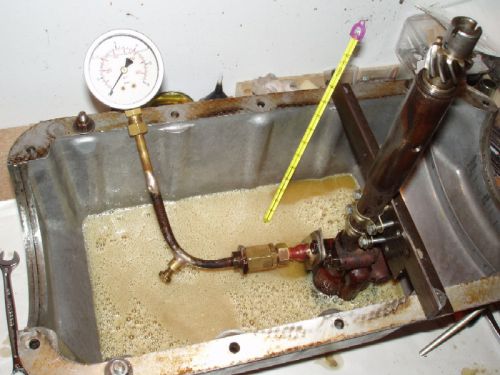
On voit bien l'émulsion créée dans l'huile par le retour du jet sous pression.
Par sécurité, il a été utilisé une huile de viscosité immédiatement inférieure à celle qui sera utilisée plus tard dans le moteur (15W40 au lieu de 20W50).
La pompe se règle, une fois son bon fonctionnement vérifié, par la vis creuse servant de butée au ressort antagoniste du clapet de décharge.
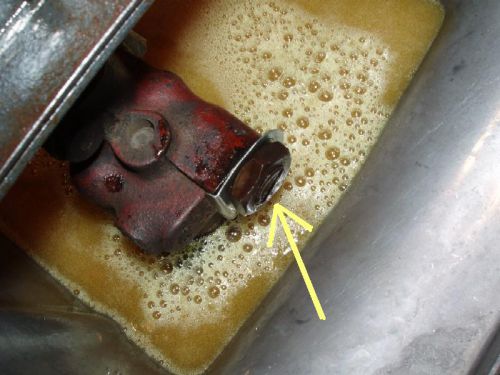
En augmentant la vitesse d'entrainement de la pompe, on distingue bien au manomètre le déclenchement du clapet de décharge: La pression augmente linéairement, puis se stabilise.
Le réglage reste toutefois d'une précision assez moyenne, et il faudra surtout vérifier la bonne et rapide montée en pression de la pompe aux régimes faibles. Dés l'entrainement à la main, le jet d'huile doit être franc en sortie du gicleur.
Aux environs de 2000 T/min à la pompe, nous obtenons 4,5 Kg de pression, ce qui est satisfaisant.
Serrer le contre-écrou et rabattre le frein tôle, la pompe est prête pour un long usage.
Il s'agit maintenant de la monter à sa bonne place:
- Vérifier d'abord que le bloc est bien muni des deux olives en entrée des canalisations d'huile.

- Monter la tubulure d'huile en engageant seulement quelques filets des écrous de serrage, pour que l'ensemble puisse bouger un peu.
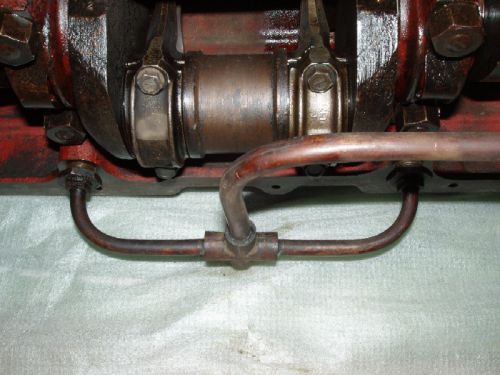
- Placer le moteur au P.M.H. fin de compression du cylindre n°1
- Dans cette position exacte, engager la pompe à huile dans le bloc,
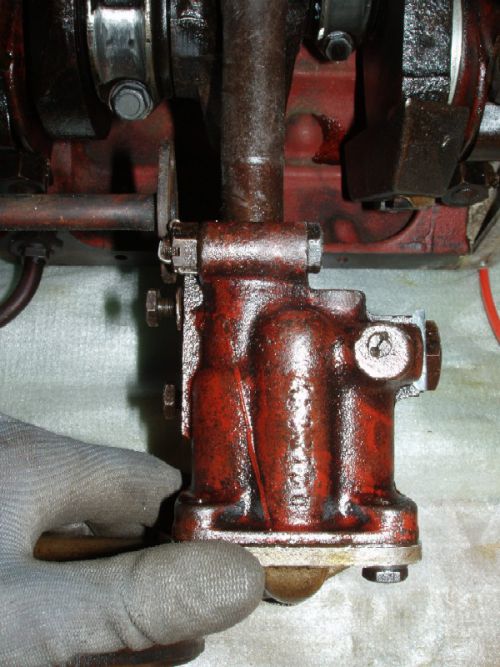
de façon à ce qu'en fin d'engrènement sur l'arbre à cames, elle finisse avec la fente du pignon de commande parallèle au bloc moteur, et le petit coté ou "petite lune" orienté vers l'arbre à cames, soit la "grande lune" vers l'extérieur.
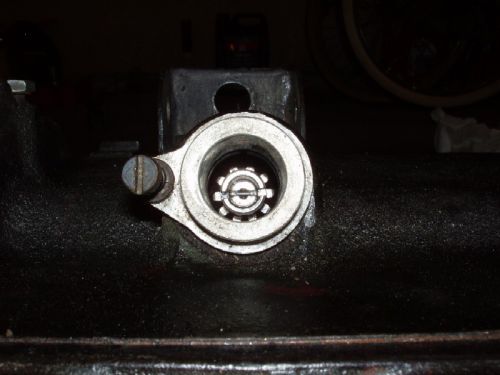
C'est une convention de calage sur les moteurs de tractions, et c'est à cette position que l'allumeur aura son rotor orienté vers le plot de sortie H.T. du cylindre 1 lors de son remontage.
- Placer alors la vis pointée de maintien de la pompe, sur le bloc, bien engagée dans le trou du tube de pompe (vérifier l'alignement des trous avant)
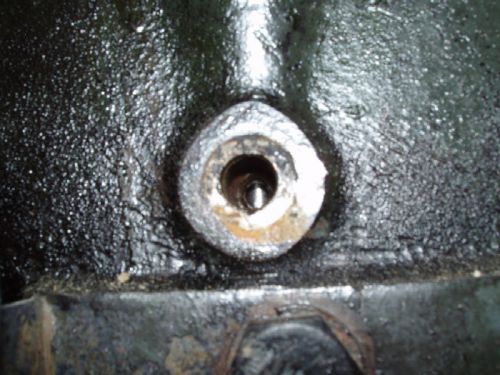
et la serrer modérément (1,5 m.Kg maxi).
Bien serrer, par contre, son contre-écrou (3 m.Kg).
- Finir de fixer la tubulure d'huile sur pompe, avec son joint papier, serrer les vis et freiner.
- Terminer par le serrage des écrous de tubulure sur bloc: 6 m.kg pour l'écrou raccord
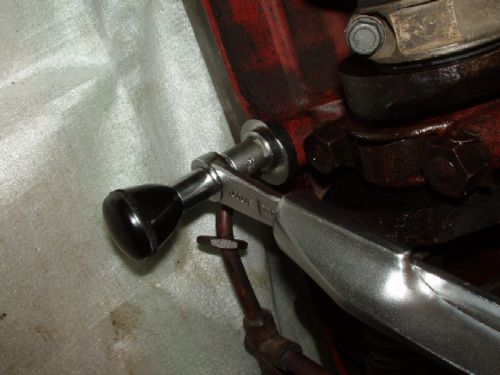
et de leurs contre-écrous: 4 m.kg
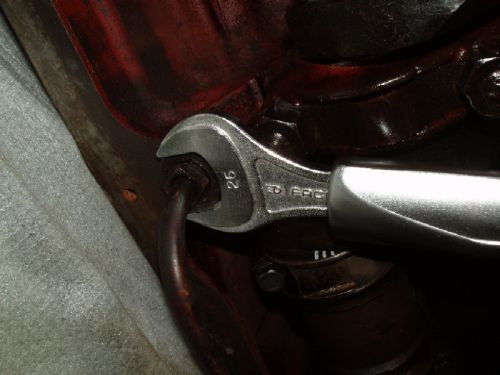
C'est terminé coté pompe !
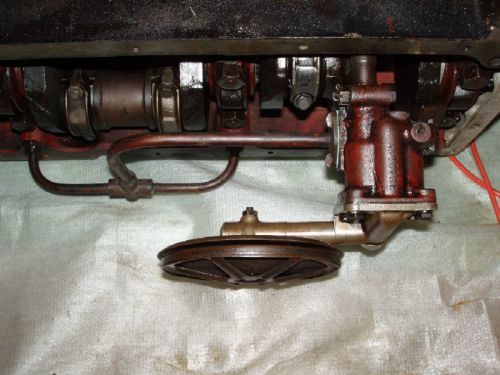
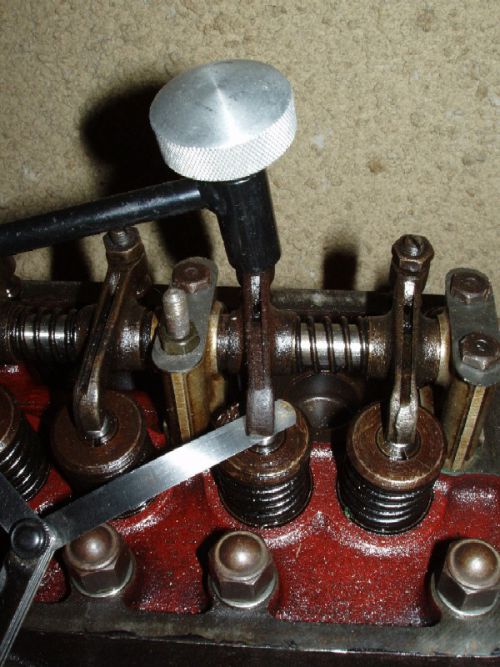
Bon, en haut du moteur, ça commence à être bon, il est temps de passer à la partie basse où le remontage de la pompe à huile reste à faire.
Préalablement, nous allons la tarer, et surtout vérifier son bon fonctionnement avec un montage très proche de celui décrit dans le M.R. (manuel des réparations) du constructeur.
(Encore merci à Julien et Jean Christophe pour le prêt du banc d'essais)
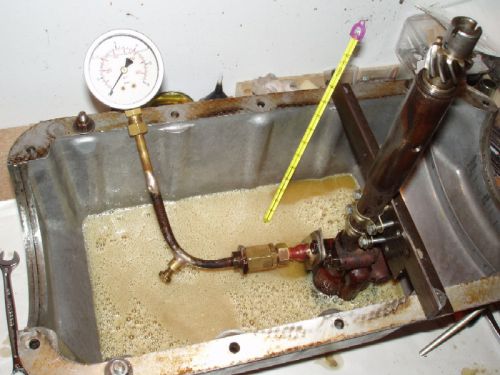
On voit bien l'émulsion créée dans l'huile par le retour du jet sous pression.
Par sécurité, il a été utilisé une huile de viscosité immédiatement inférieure à celle qui sera utilisée plus tard dans le moteur (15W40 au lieu de 20W50).
La pompe se règle, une fois son bon fonctionnement vérifié, par la vis creuse servant de butée au ressort antagoniste du clapet de décharge.
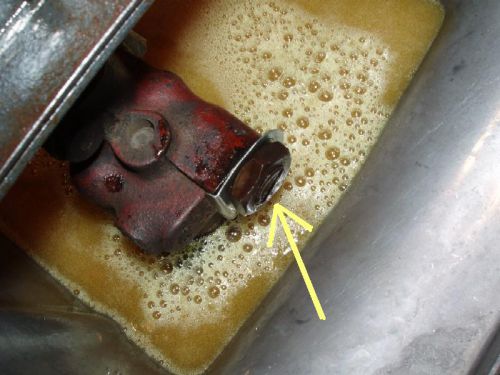
En augmentant la vitesse d'entrainement de la pompe, on distingue bien au manomètre le déclenchement du clapet de décharge: La pression augmente linéairement, puis se stabilise.
Le réglage reste toutefois d'une précision assez moyenne, et il faudra surtout vérifier la bonne et rapide montée en pression de la pompe aux régimes faibles. Dés l'entrainement à la main, le jet d'huile doit être franc en sortie du gicleur.
Aux environs de 2000 T/min à la pompe, nous obtenons 4,5 Kg de pression, ce qui est satisfaisant.
Serrer le contre-écrou et rabattre le frein tôle, la pompe est prête pour un long usage.
Il s'agit maintenant de la monter à sa bonne place:
- Vérifier d'abord que le bloc est bien muni des deux olives en entrée des canalisations d'huile.

- Monter la tubulure d'huile en engageant seulement quelques filets des écrous de serrage, pour que l'ensemble puisse bouger un peu.
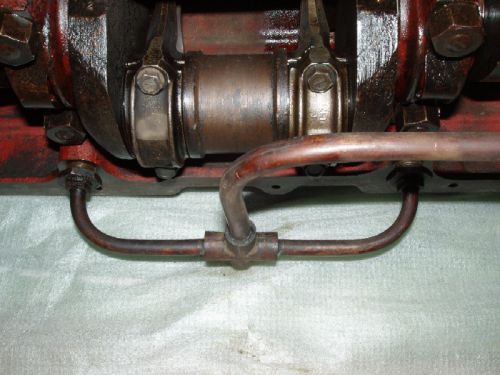
- Placer le moteur au P.M.H. fin de compression du cylindre n°1
- Dans cette position exacte, engager la pompe à huile dans le bloc,
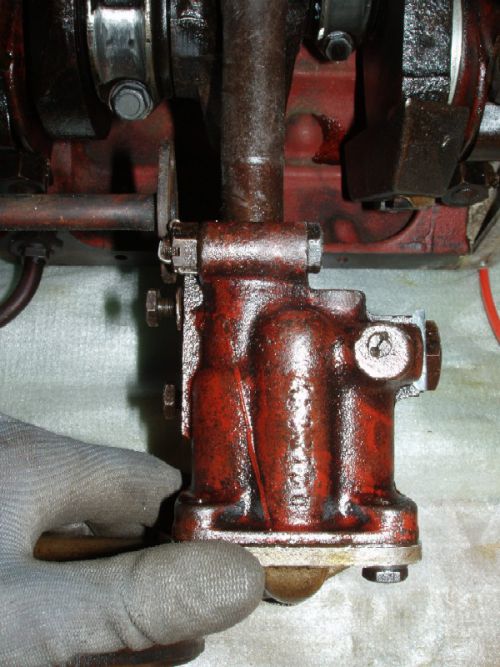
de façon à ce qu'en fin d'engrènement sur l'arbre à cames, elle finisse avec la fente du pignon de commande parallèle au bloc moteur, et le petit coté ou "petite lune" orienté vers l'arbre à cames, soit la "grande lune" vers l'extérieur.
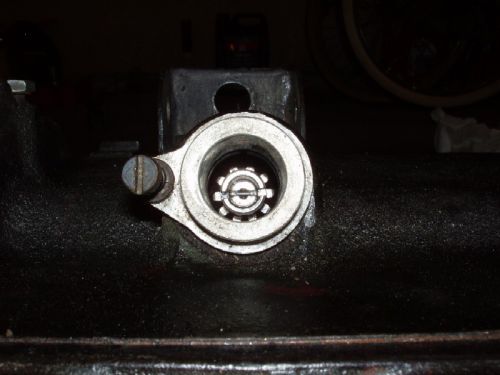
C'est une convention de calage sur les moteurs de tractions, et c'est à cette position que l'allumeur aura son rotor orienté vers le plot de sortie H.T. du cylindre 1 lors de son remontage.
- Placer alors la vis pointée de maintien de la pompe, sur le bloc, bien engagée dans le trou du tube de pompe (vérifier l'alignement des trous avant)
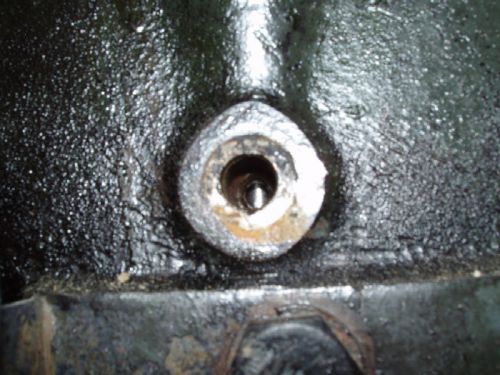
et la serrer modérément (1,5 m.Kg maxi).
Bien serrer, par contre, son contre-écrou (3 m.Kg).
- Finir de fixer la tubulure d'huile sur pompe, avec son joint papier, serrer les vis et freiner.
- Terminer par le serrage des écrous de tubulure sur bloc: 6 m.kg pour l'écrou raccord
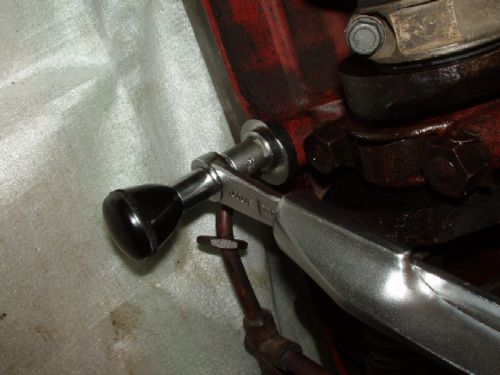
et de leurs contre-écrous: 4 m.kg
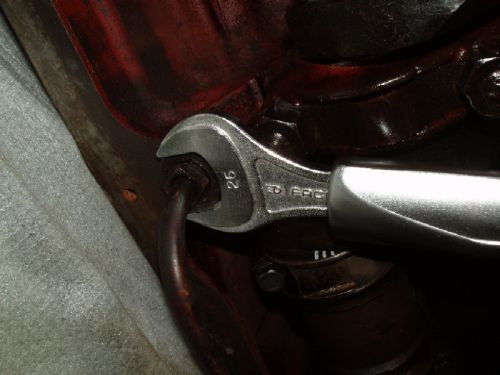
C'est terminé coté pompe !
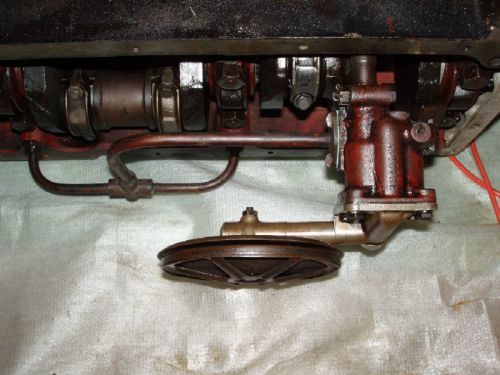
Il est temps maintenant de monter le volant, ainsi que la couronne de démarreur/damper.
Pour le volant, pas de souci de positionnement, un détrompeur existe et n'autorise qu'une seule position..
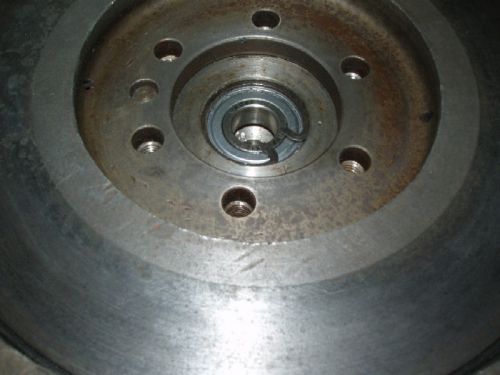
Pour le volant, pas de souci de positionnement, un détrompeur existe et n'autorise qu'une seule position..
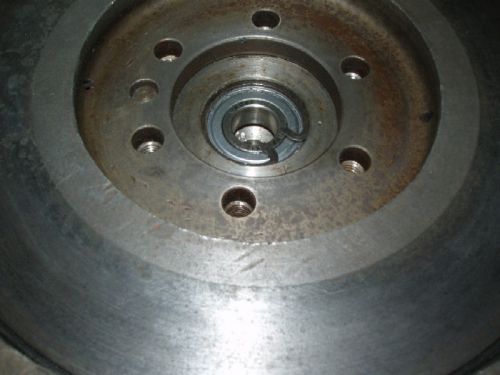
On replace un arrêtoir neuf, les vis enduites de frein filet, et serrage au couple en plaçant une cale en bois sous un maneton du vilebrequin pour bloquer la rotation.
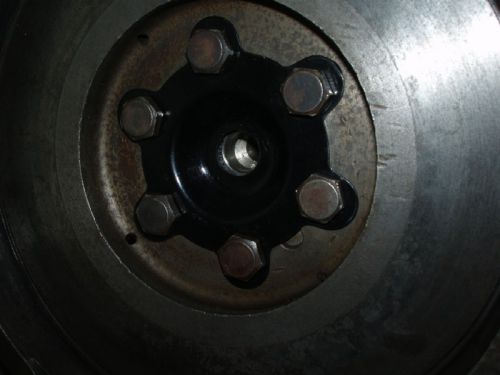
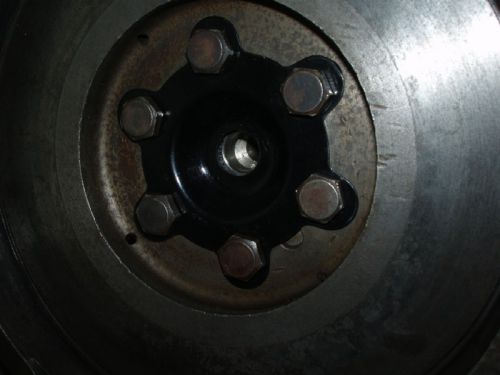
On rabat les pans de l'arrêtoir et c'est fini coté volant.
Passons de l'autre coté du moteur.
Le remontage du damper ne présente aucune difficulté. Il faut simplement bien aligner les repères faits au démontage, vérifier le bon état des frictions en "FERODO".
Comme indiqué plus haut, le serrage se fait avec un écrou de 46 sur plats, en lieu et place de l'écrou à créneaux d'origine. La douille de 46 passe juste dans le damper, et le serrage se fait puissamment, vilebrequin toujours immobilisé par une cale en bois sous le maneton le plus proche. Mettre du frein filets abondamment sur les filets de l'écrou et s'assurer à la mise en place du moyeu de damper que les clavettes restent bien en place.
Les arrêtoirs spécifiques à l'écrou à créneaux servent également au 6 pans.
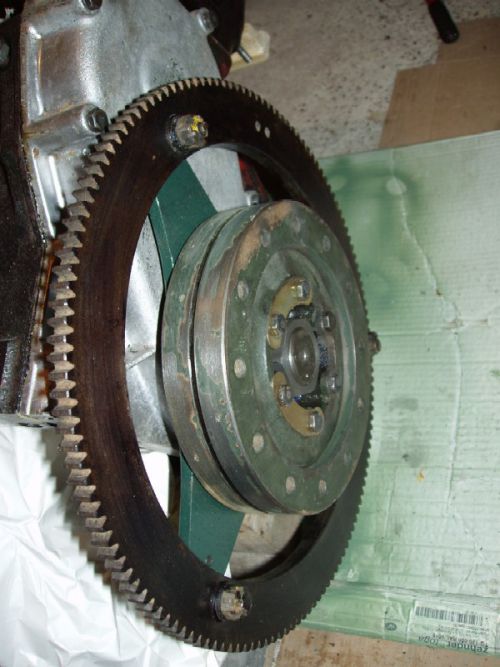
A ce stade, c'est serré devant, dessous et derrière: Il est temps de refermer ce bel ensemble avec le carter inférieur après une dernière vérification.
On reprend la séquence désormais bien rodée de l'hermétic, joint, re-Hermétic...
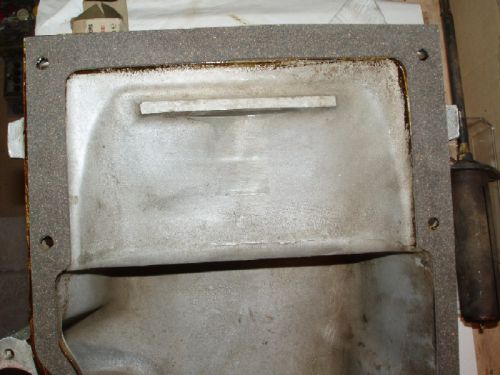
Et voilà le carter en place, adieu au bel embiellage, qu'on ne souhaite pourtant pas revoir de sitôt !
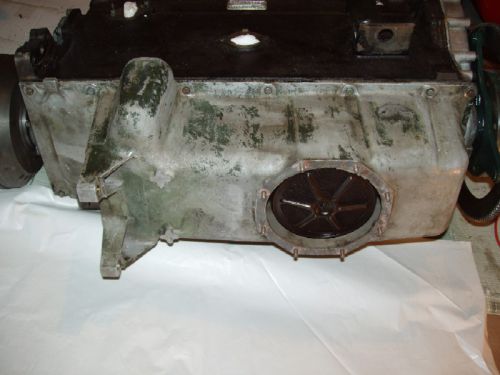
Passons de l'autre coté du moteur.
Le remontage du damper ne présente aucune difficulté. Il faut simplement bien aligner les repères faits au démontage, vérifier le bon état des frictions en "FERODO".
Comme indiqué plus haut, le serrage se fait avec un écrou de 46 sur plats, en lieu et place de l'écrou à créneaux d'origine. La douille de 46 passe juste dans le damper, et le serrage se fait puissamment, vilebrequin toujours immobilisé par une cale en bois sous le maneton le plus proche. Mettre du frein filets abondamment sur les filets de l'écrou et s'assurer à la mise en place du moyeu de damper que les clavettes restent bien en place.
Les arrêtoirs spécifiques à l'écrou à créneaux servent également au 6 pans.
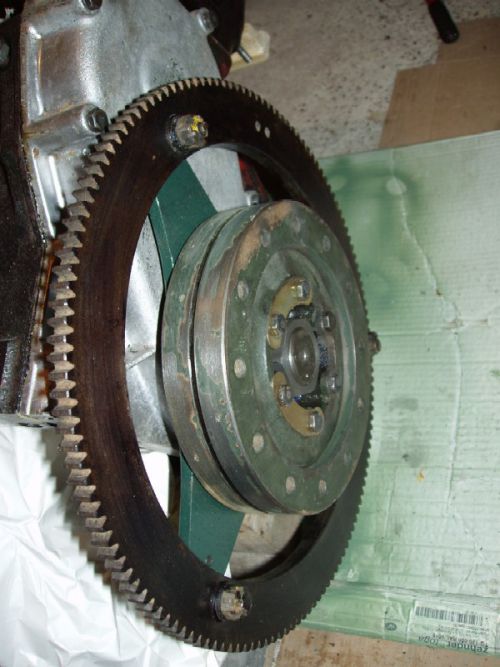
A ce stade, c'est serré devant, dessous et derrière: Il est temps de refermer ce bel ensemble avec le carter inférieur après une dernière vérification.
On reprend la séquence désormais bien rodée de l'hermétic, joint, re-Hermétic...
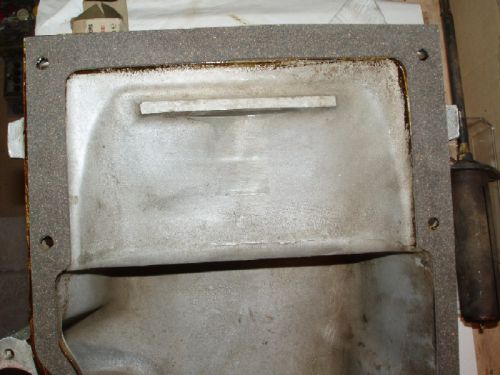
Et voilà le carter en place, adieu au bel embiellage, qu'on ne souhaite pourtant pas revoir de sitôt !
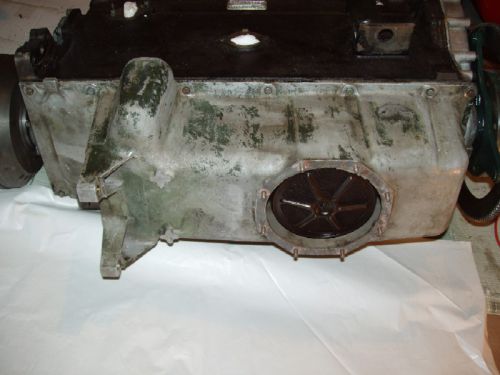
A partir de maintenant, on ne touche plus à la vis centrale maintenant la crépine de pompe à huile. La dévisser impose de démonter le carter inférieur pour pouvoir la revisser et maintenir son contre écrou.
La plaque inférieure de fermeture du carter est reposée:
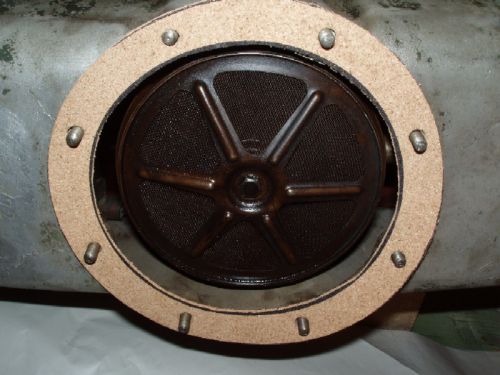
Avec un joint liège (voir article correspondant).
On serre modérément les écrous pour ne pas écraser trop le joint, sans oublier le bouchon de vidange et son joint métalloplastique.
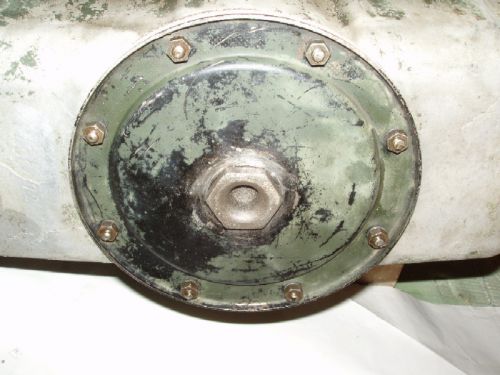
On peut désormais reposer le moteur à l'endroit !
Et reposer la poulie d'entrainement de dynamo et pompe à eau (Fantomas participe !) :
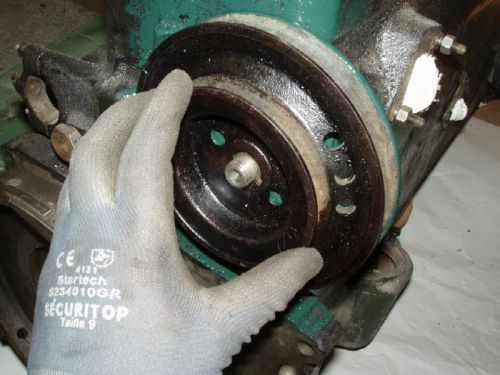
Mise en place de l'arrêtoir et serrage au couple (5,5 mKg):
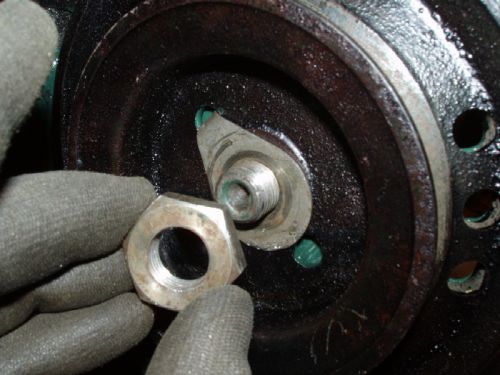
La plaque inférieure de fermeture du carter est reposée:
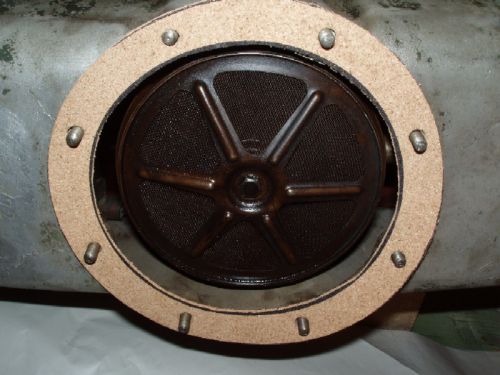
Avec un joint liège (voir article correspondant).
On serre modérément les écrous pour ne pas écraser trop le joint, sans oublier le bouchon de vidange et son joint métalloplastique.
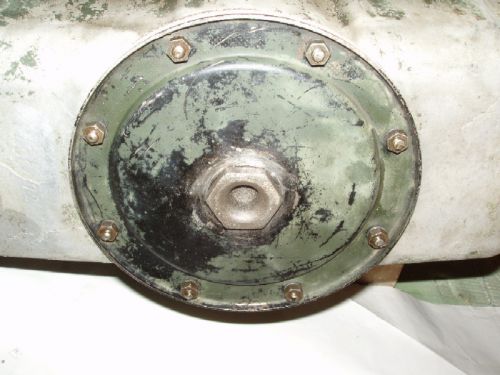
On peut désormais reposer le moteur à l'endroit !
Et reposer la poulie d'entrainement de dynamo et pompe à eau (Fantomas participe !) :
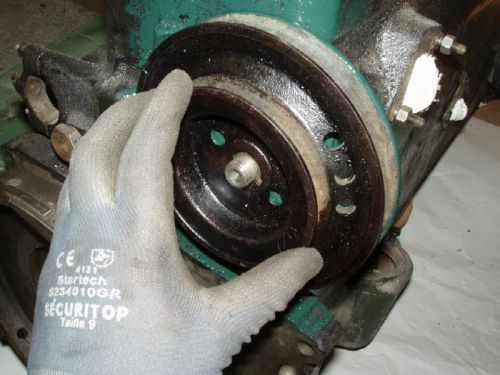
Mise en place de l'arrêtoir et serrage au couple (5,5 mKg):
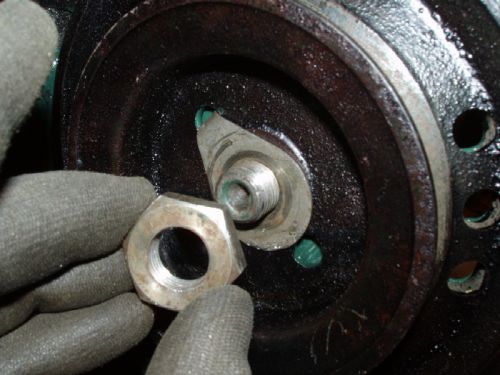
On obtient ceci, qui ressemble de plus en plus à un moteur de 15/6:
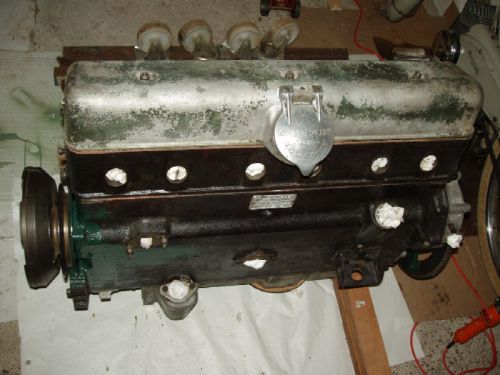
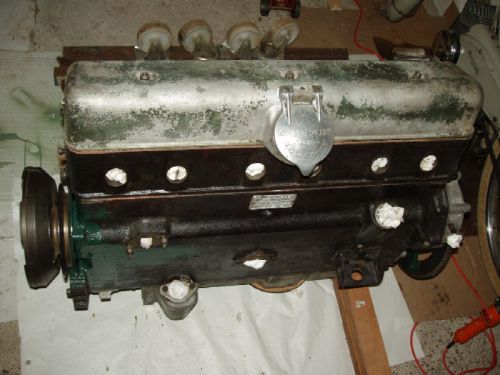
Et encore plus après une première couche de "vert moteur" :
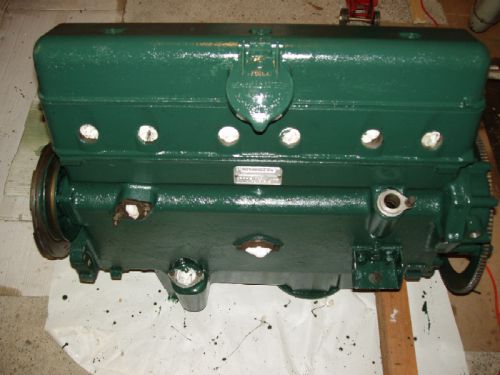
L'étape suivante va demander la fourniture d'un peu de tube carré, de 4 solides roulettes et quelques minutes de soudure à l'arc, pour un accessoire pas très esthétique mais bien pratique:
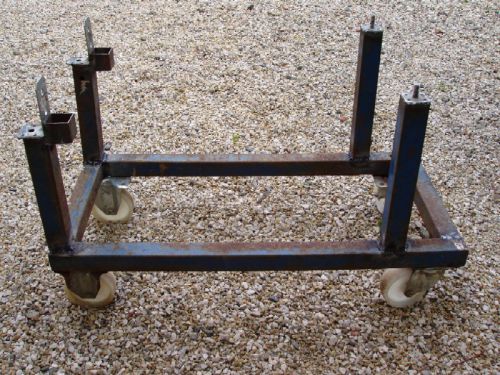
On en profite pour faire la deuxième couche, au pistolet (la nuance du vert, parfaitement conforme à l'origine est altérée par le flash) :
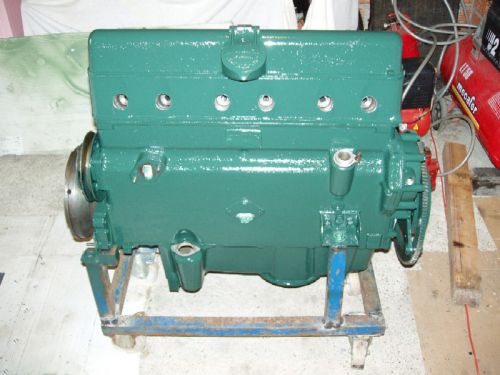
Il est bien joli ce moteur sur son support, mais encore un peu nu finalement.
Montons les derniers accessoires, La pipe de sortie d'eau:
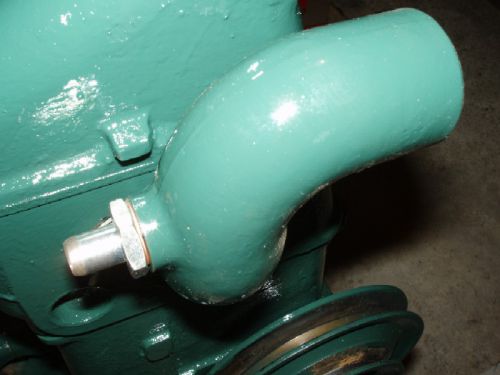
La jauge d'huile, dont le flotteur liège a été refait à l'aide d'un gros bouchon retaillé et enduit de résine époxy:
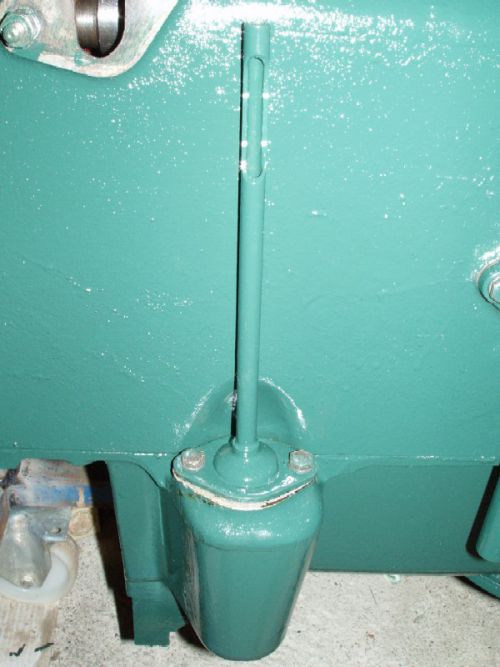
Et également le reniflard, sans oublier d'orienter la languette de la plaque intermédiaire vers le haut afin de créer une chicane pour les vapeurs d'huile:
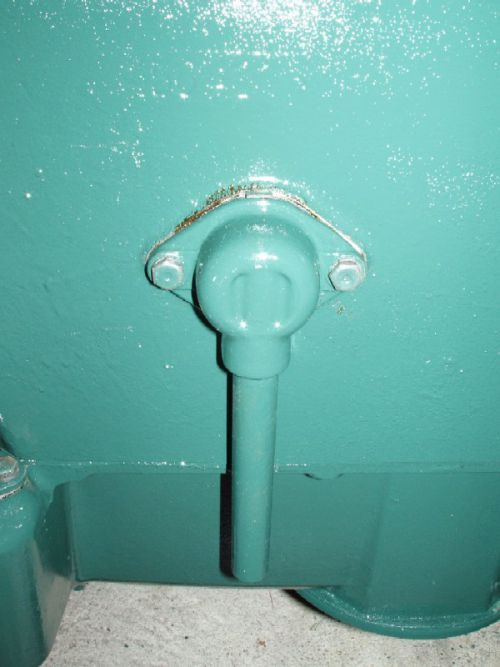
Placer la tubulure de sortie d'eau du bloc, avec comme pour les éléments précédents des joints neufs enduits d'hermétic.
Après séchage de la pâte à joints, on pourra faire de petites retouches de peinture au pinceau afin de conserver au moteur une belle unité d'aspect.
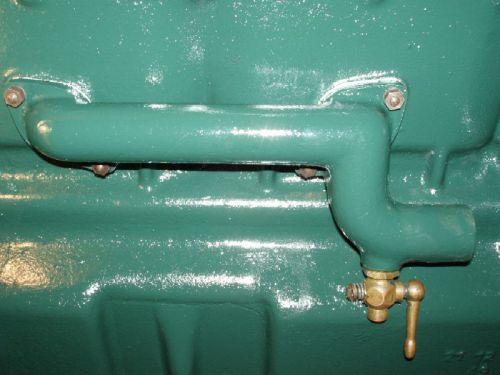
Placer les joints de collecteur d'admission/échappement, éventuellement légèrement retouchés pour bien se placer en face des trous, et enduits d'huile comme le joint de culasse.
Les goujons, eux, seront enduits de graisse Belleville, ou encore mieux de graisse cuivrée haute température. Cela va fumer un peu à la remise en route, il ne faudra pas s'inquiéter.
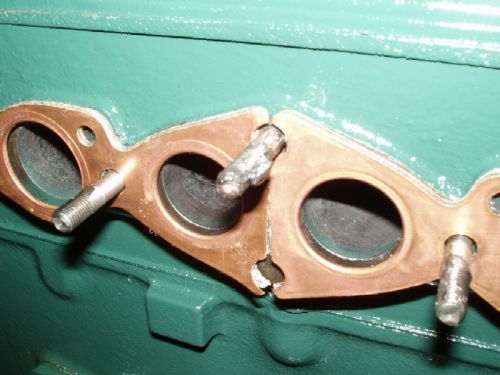
Présenter le collecteur complet, préalablement préparé et dont la planeîté aura été vérifiée:
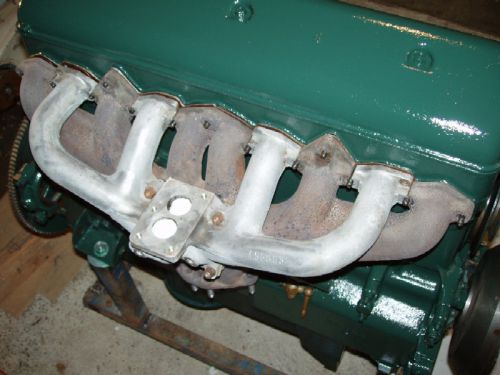
Il doit se présenter sans contrainte sur ses goujons, jusqu'en butée sur la culasse.
Les collecteurs de 15/6 sont assez fragiles, du fait de leur taille, et il faut procéder à leur serrage de manière très progressive en commençant par le centre, puis alternativement vers les deux extrémités.
Nous serrons à 2m.Kg, après une premiere passe à 1 m.Kg.

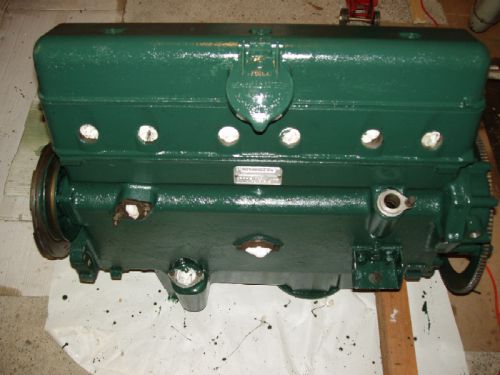
L'étape suivante va demander la fourniture d'un peu de tube carré, de 4 solides roulettes et quelques minutes de soudure à l'arc, pour un accessoire pas très esthétique mais bien pratique:
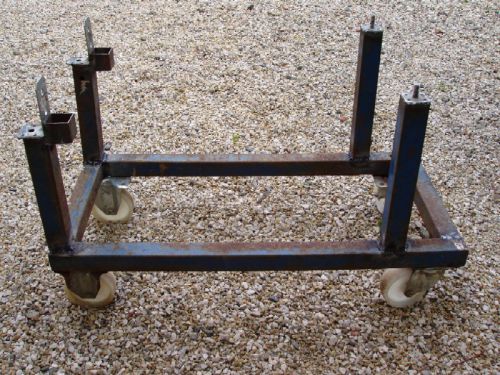
On en profite pour faire la deuxième couche, au pistolet (la nuance du vert, parfaitement conforme à l'origine est altérée par le flash) :
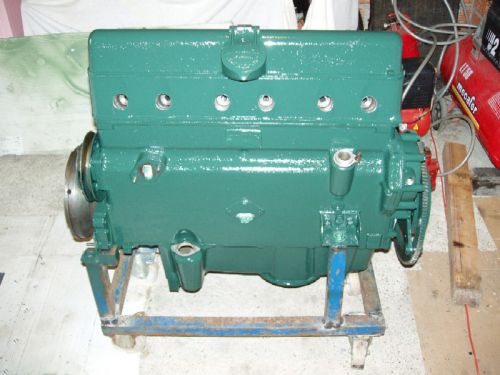
Il est bien joli ce moteur sur son support, mais encore un peu nu finalement.
Montons les derniers accessoires, La pipe de sortie d'eau:
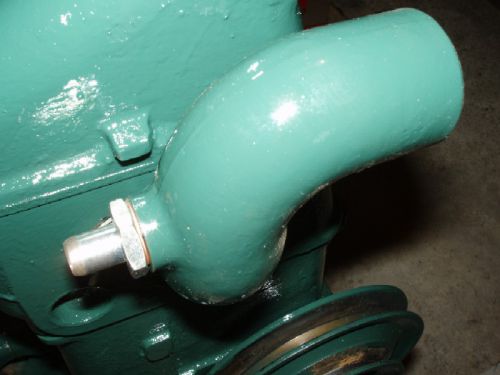
La jauge d'huile, dont le flotteur liège a été refait à l'aide d'un gros bouchon retaillé et enduit de résine époxy:
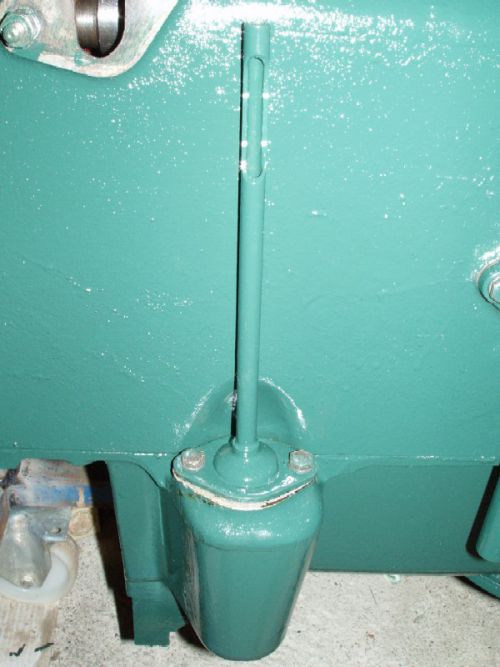
Et également le reniflard, sans oublier d'orienter la languette de la plaque intermédiaire vers le haut afin de créer une chicane pour les vapeurs d'huile:
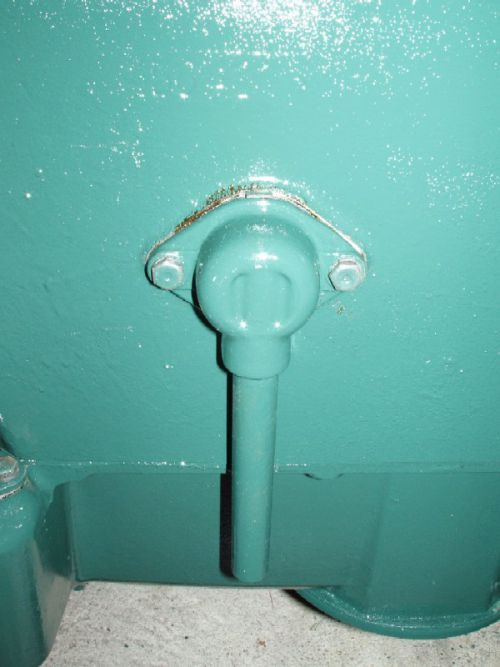
Placer la tubulure de sortie d'eau du bloc, avec comme pour les éléments précédents des joints neufs enduits d'hermétic.
Après séchage de la pâte à joints, on pourra faire de petites retouches de peinture au pinceau afin de conserver au moteur une belle unité d'aspect.
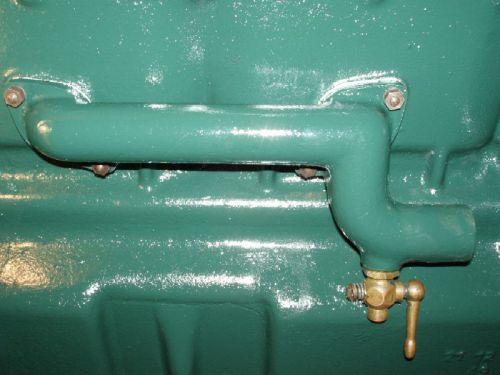
Placer les joints de collecteur d'admission/échappement, éventuellement légèrement retouchés pour bien se placer en face des trous, et enduits d'huile comme le joint de culasse.
Les goujons, eux, seront enduits de graisse Belleville, ou encore mieux de graisse cuivrée haute température. Cela va fumer un peu à la remise en route, il ne faudra pas s'inquiéter.
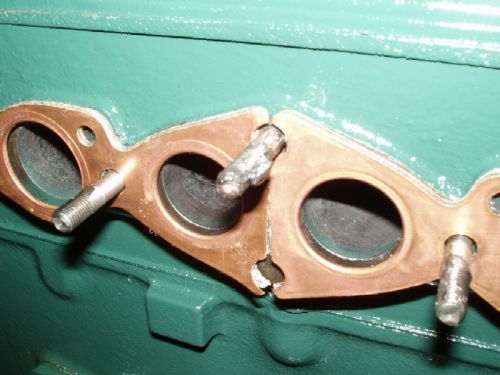
Présenter le collecteur complet, préalablement préparé et dont la planeîté aura été vérifiée:
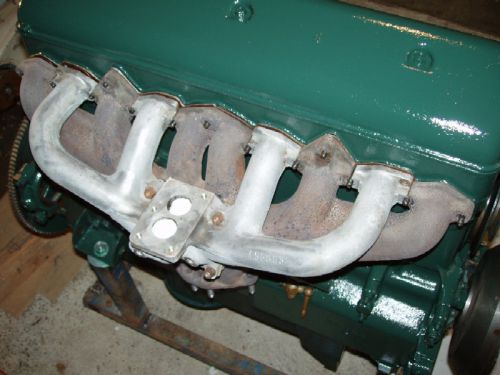
Il doit se présenter sans contrainte sur ses goujons, jusqu'en butée sur la culasse.
Les collecteurs de 15/6 sont assez fragiles, du fait de leur taille, et il faut procéder à leur serrage de manière très progressive en commençant par le centre, puis alternativement vers les deux extrémités.
Nous serrons à 2m.Kg, après une premiere passe à 1 m.Kg.

Voilà, c'est serré et en bonne place. Une pièce magnifique !
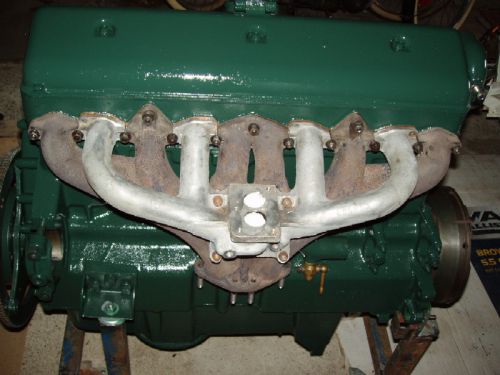
Nous n'avons pas encore placé l'écran alu d'isolation thermique. En réfection, il sera placé plus tard, après les tous premiers essais du moteur.
Ne pas oublier l'indispensable tubulure de graissage de la rampe des culbuteurs:
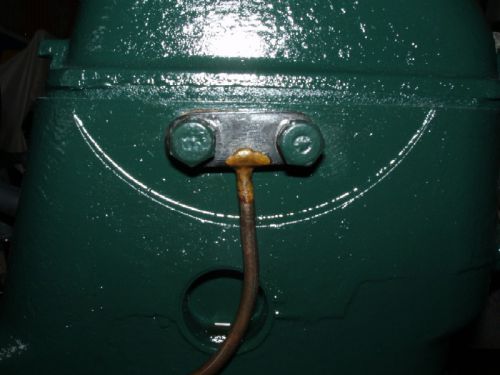
Place maintenant à la pompe à essence, une alliée fidèle des voraces 6 cylindres.
Elle a, comme tous les accessoires, été reconditionnée à part.
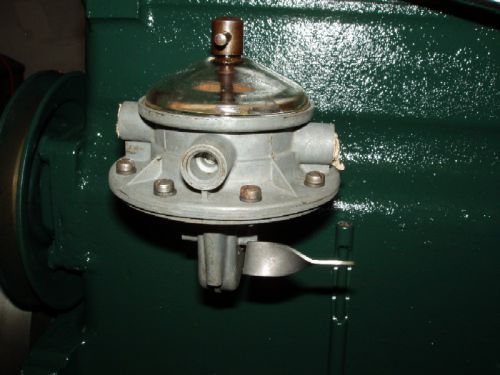
Et, à l'autre bout, le carburateur, avec sa séquence de joints correcte depuis la tubulure: 1 joint Hugo Reinz, 1 cale épaisse fibre, 1 joint Hugo Reinz, le carburateur.
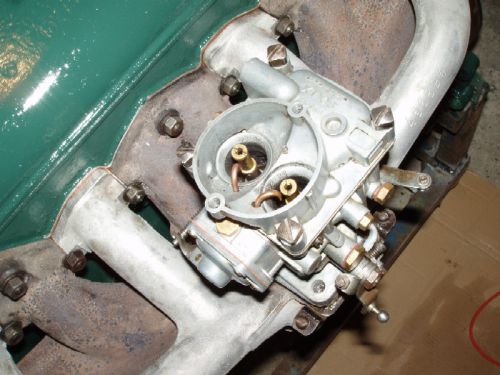
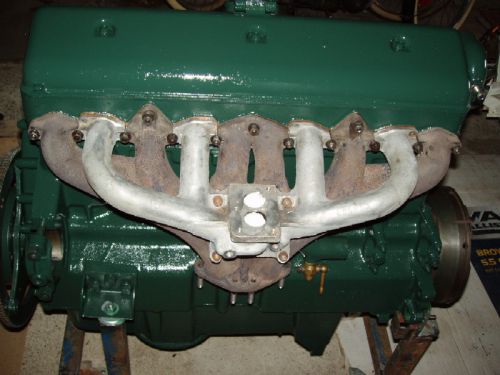
Nous n'avons pas encore placé l'écran alu d'isolation thermique. En réfection, il sera placé plus tard, après les tous premiers essais du moteur.
Ne pas oublier l'indispensable tubulure de graissage de la rampe des culbuteurs:
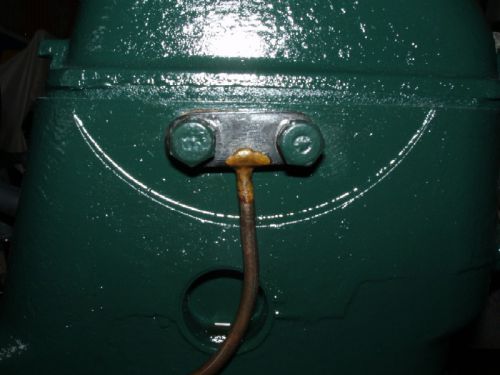
Place maintenant à la pompe à essence, une alliée fidèle des voraces 6 cylindres.
Elle a, comme tous les accessoires, été reconditionnée à part.
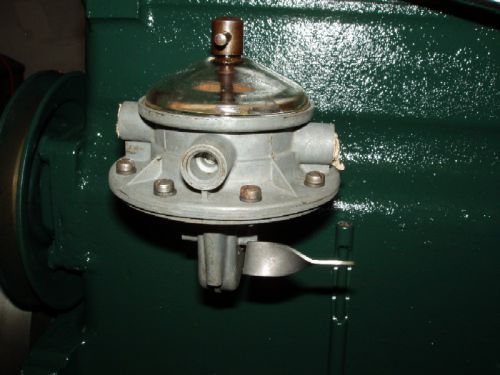
Et, à l'autre bout, le carburateur, avec sa séquence de joints correcte depuis la tubulure: 1 joint Hugo Reinz, 1 cale épaisse fibre, 1 joint Hugo Reinz, le carburateur.
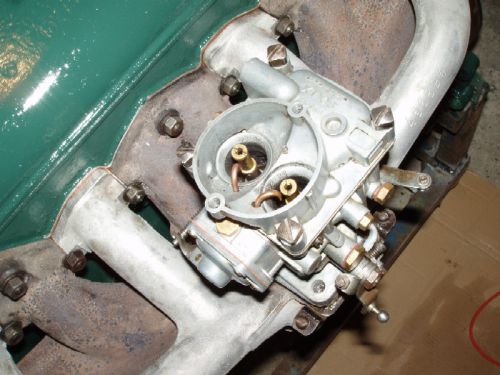
Bien entendu, pour engloutir et brûler toute cette essence, l'allumeur est indispensable.
On le remonte selon la procédure décrite dans l'article sur l'allumage.
Il n'est pas inutile de repérer, sur le distributeur, la correspondance des plots avec les cylindres. Cela facilitera un éventuel démontage futur.
On replace aussi le faisceau, qu'on aura pu confectionner selon la méthode décrite également en article.
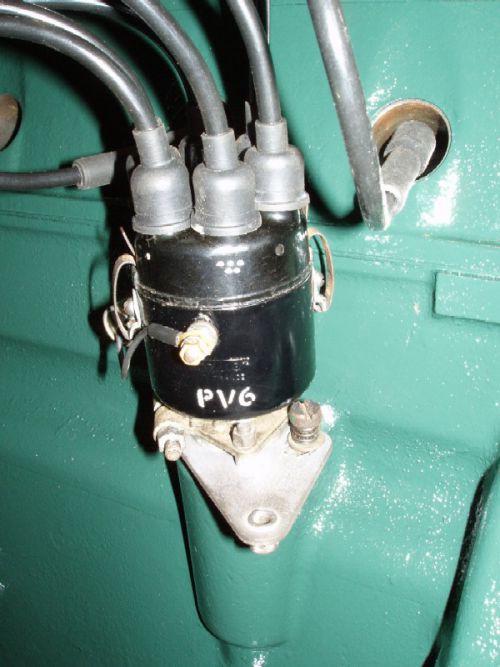
On le remonte selon la procédure décrite dans l'article sur l'allumage.
Il n'est pas inutile de repérer, sur le distributeur, la correspondance des plots avec les cylindres. Cela facilitera un éventuel démontage futur.
On replace aussi le faisceau, qu'on aura pu confectionner selon la méthode décrite également en article.
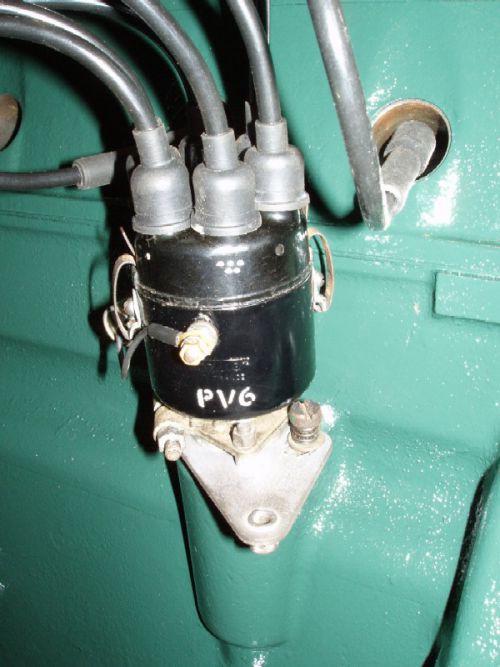
On remonte 6 bougies neuves, on connecte le faisceau sans se tromper, et on obtient ceci:
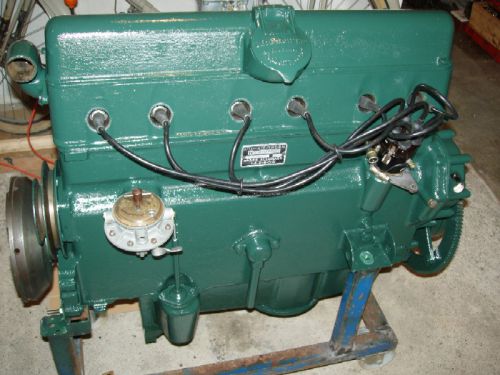
Prêt à pousser son premier cri ?
Pas tout à fait, il manque encore quelques éléments indispensables ...
Le démarreur, bien entendu, reconditionné mais pas encore repeint. Il recevra sa décoration après les premiers essais:
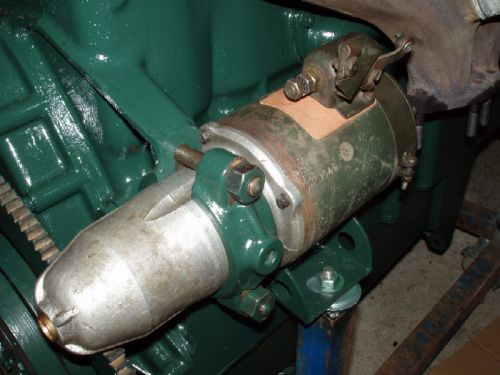
Et on n'oublie surtout pas le plein d'huile !
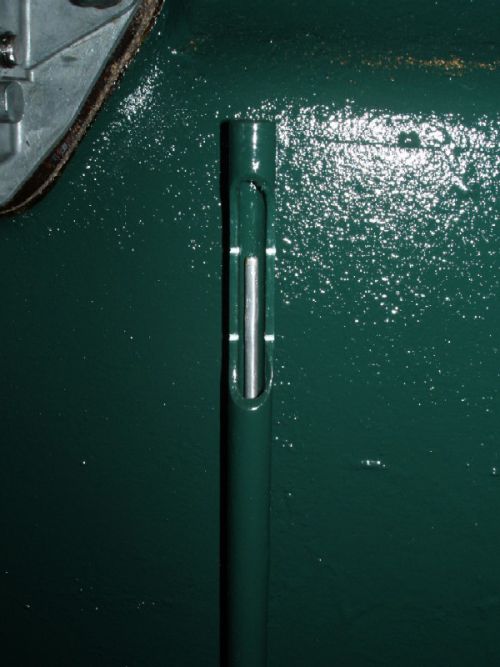
L'impression est énorme, en échappement libre, et il faut vite interrompre l'expérience, car il n'y a pas de radiateur de refroidissement, donc pas question de le faire tourner plus de quelques dizaines de secondes, soit juste le temps de vider la cuve du carburateur...
La vidéo est visible à l'adresse suivante:
www.dailymotion.com/video/xjwubk_video-156_auto
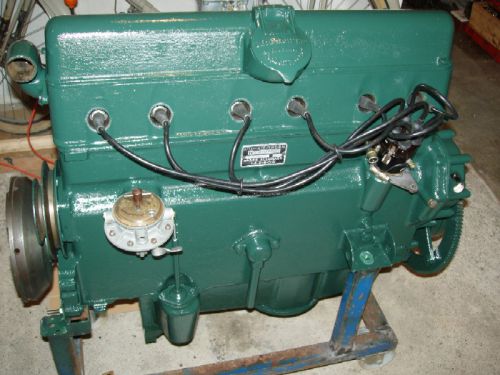
Prêt à pousser son premier cri ?
Pas tout à fait, il manque encore quelques éléments indispensables ...
Le démarreur, bien entendu, reconditionné mais pas encore repeint. Il recevra sa décoration après les premiers essais:
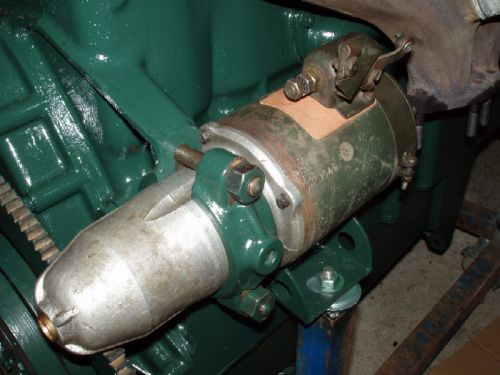
Et on n'oublie surtout pas le plein d'huile !
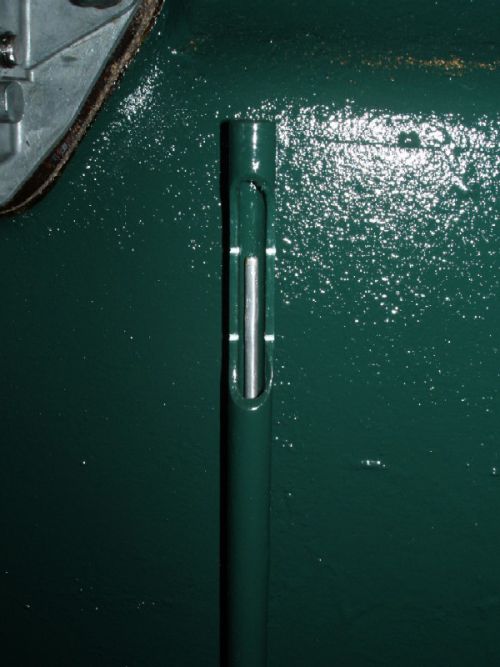
Voilà, l'histoire de cette restauration s'achève le 04 juillet 2011: le moteur démarre au banc, au 4° coup de démarreur et se stabilise rapidement sur un ralenti impeccable.
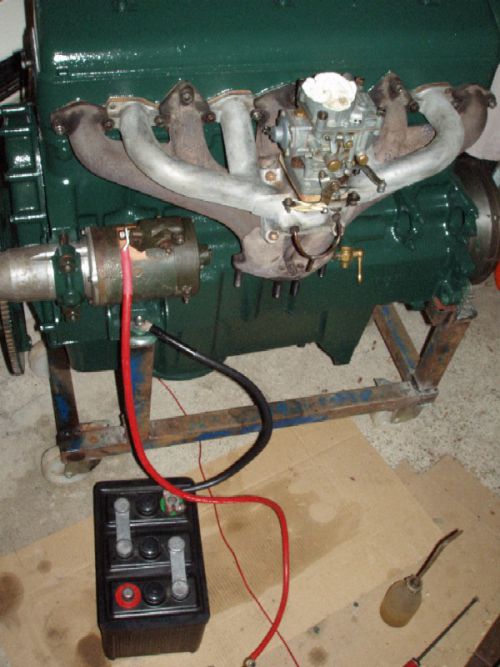
L'impression est énorme, en échappement libre, et il faut vite interrompre l'expérience, car il n'y a pas de radiateur de refroidissement, donc pas question de le faire tourner plus de quelques dizaines de secondes, soit juste le temps de vider la cuve du carburateur...
La vidéo est visible à l'adresse suivante:
www.dailymotion.com/video/xjwubk_video-156_auto
Il suffit maintenant d'accoupler la boite, et l'ensemble est prêt au remontage dans la caisse:
Article ajouté le 2010-09-08 , consulté 1267 fois
⨯
Inscrivez-vous au blog
Soyez prévenu par email des prochaines mises à jour
Rejoignez les 350 autres membres